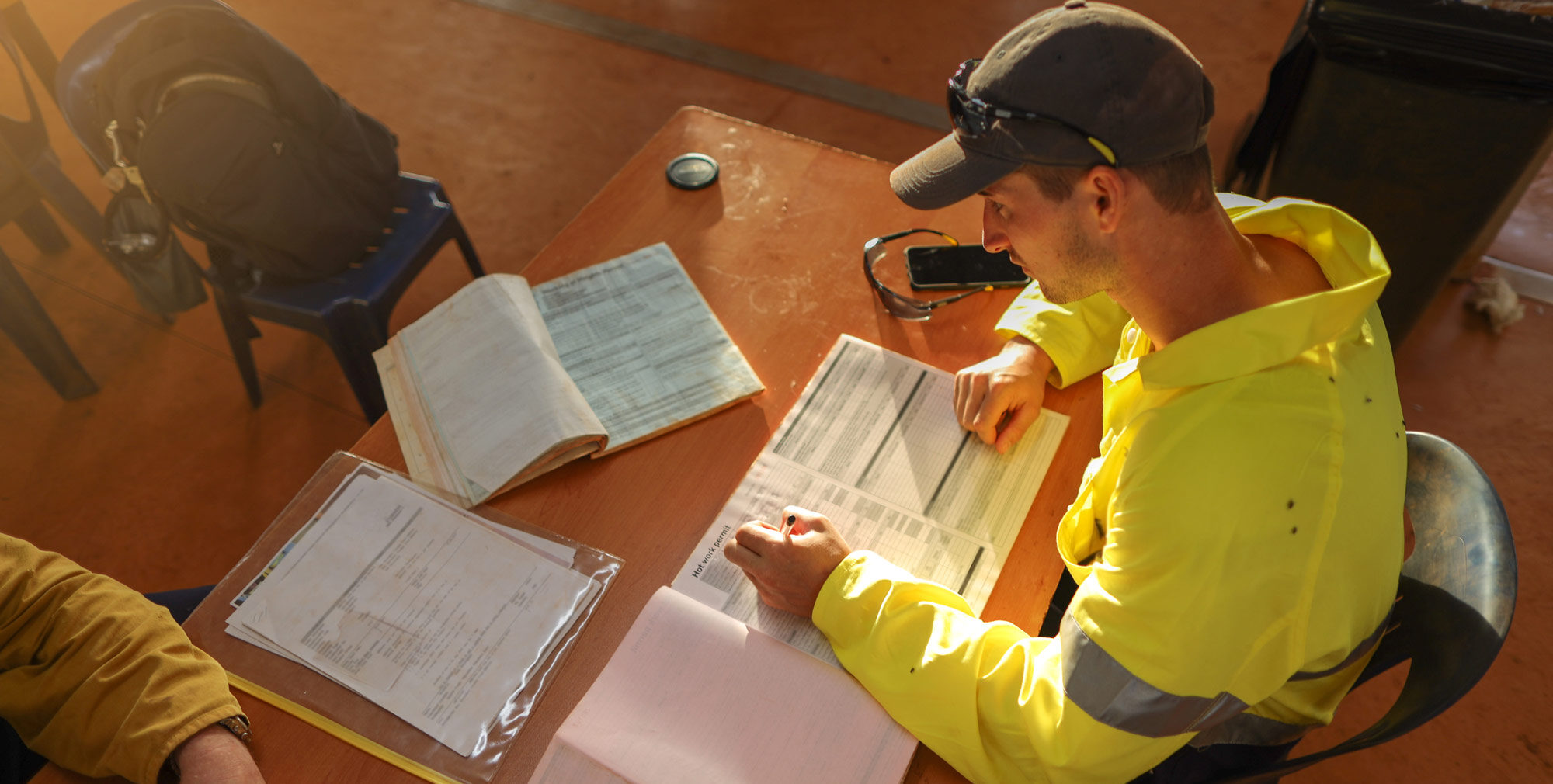
6 steps to conduct a job hazard analysis for workplace safety
Effective workplace safety hinges on proactively identifying risks before they become accidents. While it’s important to analyze as many jobs as possible, time and resources are often limited. A job hazard analysis (JHA), sometimes called job safety analysis (JSA), makes it easier to identify which tasks within jobs have the greatest potential dangers. Concentrating on these high-risk jobs first can ensure that your safety efforts are strategic and impactful, helping to protect your team from preventable accidents. In this blog post, we’ll walk you through the key steps of a JHA and how to maximize its impact on your organization.
What is a JHA?
A job hazard analysis systematically identifies and controls hazards in specific job tasks. It breaks jobs into steps to prevent workplace injuries and illnesses by mitigating risks before they cause an incident.
What’s an example of JHA?
Imagine a warehouse where workers operate forklifts to move pallets. A JHA for this task would involve:
- Noting the areas where forklifts will be used.
- Observing forklift operation.
- Identifying hazards like collisions, tipping, or falling objects.
- Implementing safety measures such as safety training, installing protective barriers, and requiring workers to use Personal Protective Equipment (PPE) when performing tasks.
What are the steps of a JHA?
Understanding the steps in a JHA is key to successful implementation. Each step builds on the last, creating a comprehensive approach to hazard identification and mitigation. Here are the essential steps:
1. Select jobs and processes to analyze
Determine which jobs to analyze first. Focus on jobs with high injury rates, recent accidents, or complex processes. Prioritize jobs with severe potential consequences, like those involving hazardous materials or heavy machinery. By focusing on high-risk areas, you can reduce the likelihood of accidents and injuries.
2. Observe the job and list its steps
After selecting jobs, break them down into individual components. Observe the job in action and list each step, including start-up, shutdown, and maintenance. Accurate observation is crucial to identify all potential hazards.
3. Describe the hazards in each step
Identify the hazards associated with each job step. Consider environmental factors like noise and lighting, and job-specific risks, such as sharp objects or chemical exposure. This thorough analysis uncovers hidden dangers and provides a clear risk picture.
4. Develop corrective measures
Determine how to control or eliminate identified hazards. Use the hierarchy of controls, which ranges from eliminating hazards to using PPE as a last resort. For example, substitute harmful chemicals with safer alternatives, and ensure workers have appropriate protective gear if substitution isn’t possible.
5. Write safe job procedures
Document safe work practices once corrective measures are in place. Specify required PPE, outline steps to safely perform the job and make procedures accessible to all employees. Regularly review these procedures with your team to reinforce safe practices.
6. Certify, document, and keep records
The final step is to certify and document your findings. Keep detailed records of each JHA to reference later and demonstrate compliance. Regularly review and update these records to ensure your job hazard analysis remains relevant as jobs and environments evolve.
How to involve employees in a JHA
Employees bring firsthand knowledge of their job, providing valuable insights into potential hazards that management might miss. Their direct involvement makes the analysis more accurate and effective.
Create a diverse team
Building a diverse team of workers and supervisors with different expertise ensures a more thorough analysis. Workers on the front lines may notice specific safety issues related to their daily jobs, while experienced supervisors can identify broader procedural risks. This variety of perspectives helps create a comprehensive view of potential hazards.
Empowering employees through training
Training your team to conduct JHAs not only enhances their skills but also empowers them to take ownership of workplace safety. When employees are actively involved in the process, they become more invested in maintaining a safe work environment. This collaborative approach fosters a culture of shared responsibility, where safety is everyone’s priority.
Job hazard analysis (JHA) FAQ
What is the hierarchy of controls?
The hierarchy of controls is a way to tackle hazards, ranked from most to least effective:
- Elimination: Get rid of the hazard completely.
- Substitution: Swap the hazard for something safer.
- Engineering controls: Put barriers or changes in place to keep people safe.
- Administrative controls: Change how work is done to reduce exposure to the hazard.
- Personal protective equipment (PPE): Use protective gear as the last line of defense.
What specific data or criteria should I use to prioritize jobs?
Start with jobs that have a history of accidents or near-misses. Focus on those involving hazardous materials, heavy machinery, or complex steps. If a job has recently changed, like new equipment or procedures, make sure to prioritize it, too.
How often should I review and update JHAs?
Review and update your JHA whenever something changes at work, like new equipment or procedures. It’s also smart to check them annually or after any accident or close call to keep everything current.
How detailed should the written safe job procedures be?
Your procedures should be clear and concise, covering the important safety steps. Include things like what protective gear to wear and how to handle materials safely. Avoid unnecessary details, but make sure the critical information is included.
What is the best way to document and store JHA records?
Keep your records organized and easy to find. Digital tools or safety software are great for this. Store everything securely and back it up regularly. Make sure your team can easily access and update these records when needed.
Enhance workplace safety with regular JHAs
Implementing a systematic JHA is one of the most effective ways to enhance workplace safety. By following these steps, organizations can prevent accidents and foster a culture of safety and compliance.
With the right tools and training programs, your business can streamline these processes and reduce risks effectively. BLR offers software and training solutions that help businesses follow safety and legal rules, ensuring a safe and compliant workplace.
Contact us today to learn more about how BLR can support your safety initiatives.