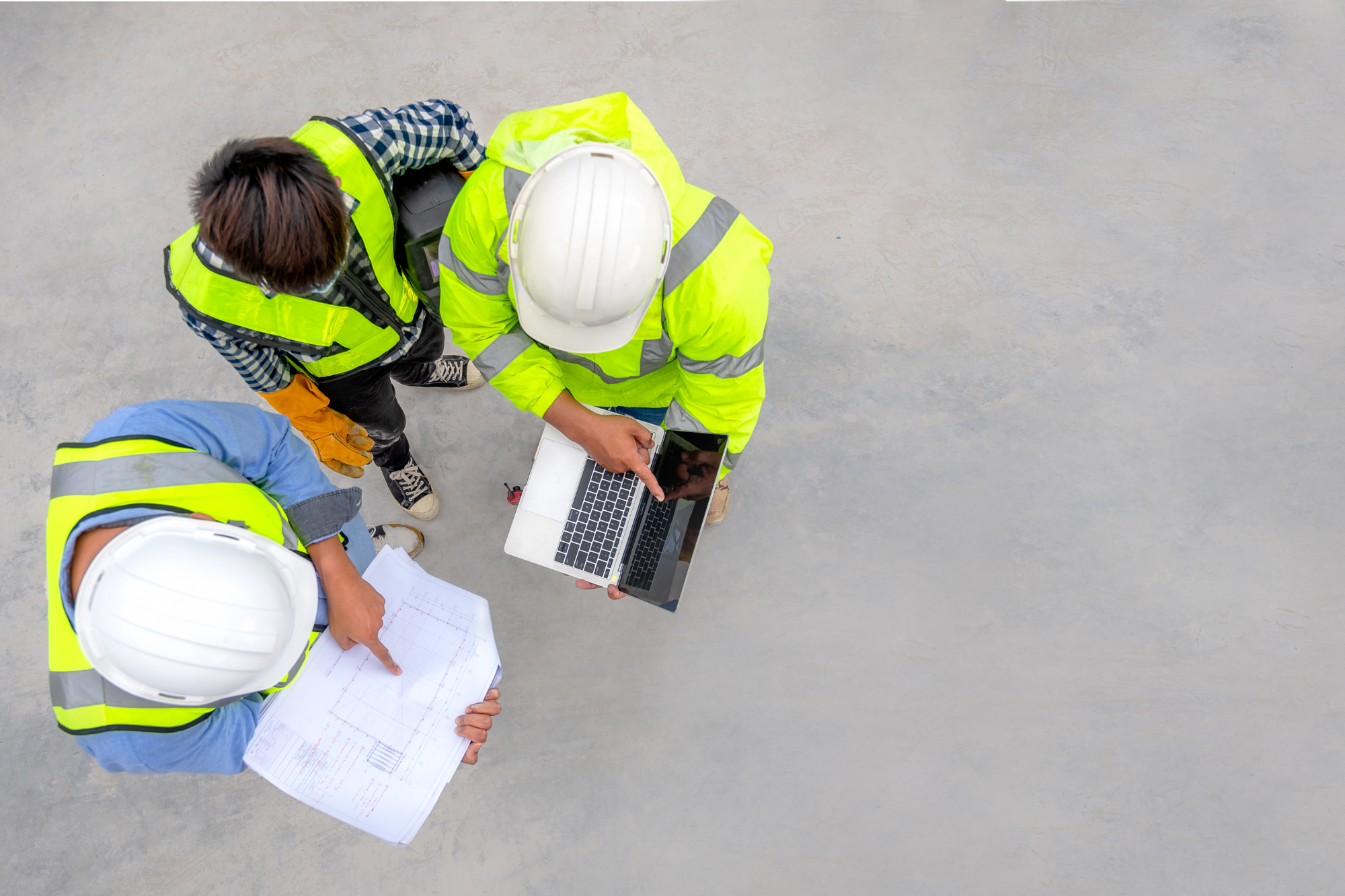
Safety audits: A cornerstone for effective EHS programs
Safety and health audits represent a proactive approach to protecting employees, improving operational efficiency, and maintaining compliance with regulations. A systematic evaluation of safety and health practices helps organizations prevent accidents, enhance workplace culture, and stay ahead of potential hazards. In this blog, we delve into why safety and health audits are indispensable, and how to develop an effective program that delivers results.
The importance of safety and health audits
A well-prepared and executed safety audit or inspection program does more than just identify risks; it builds a foundation for a safer workplace. These audits focus on uncovering unsafe conditions, equipment, or work practices before they lead to accidents or illnesses. By fostering a proactive mindset, audits:
- Inform management about the organization’s safety status.
- Use inspection time efficiently.
- Ensure consistency in recording observations.
- Reduce the chances of critical safety issues being overlooked.
Think of safety inspections as preventive maintenance—essential for both machinery and human processes. Over time, equipment wears out, and work routines can drift into unsafe territory. Regular audits keep these in check, ensuring that safe practices are followed, and potential hazards are addressed promptly.
Benefits of an effective safety audit program
The objectives of a safety audit extend beyond regulatory compliance. EHS leaders can leverage audits to achieve:
- Proactive hazard identification: Spot unsafe conditions or behaviors before incidents occur.
- Enhanced safety standards: Identify areas for improvement in safety protocols.
- Employee engagement: Encourage workers to take an active role in maintaining safety.
- Improved training effectiveness: Gauge the success of safety training initiatives.
- Preparation for external inspections: Anticipate issues that could arise during Occupational Safety and Health Administration (OSHA) or other regulatory inspections.
- Reduction in workplace injuries: Lower incident rates by addressing risks systematically.
Build a safety audit program in 7 steps
Developing a successful safety audit program involves careful planning and execution. Here are the key steps to ensure your program delivers meaningful results:
1. Determine your objectives
Start by defining what you aim to achieve through your safety audit program. Whether it’s reducing injury rates in a specific department or assessing overall safety performance, clear objectives guide the program’s design and execution.
Consider these questions:
- What areas or operations will the audits cover?
- How will findings be used to improve safety?
- What metrics will determine success?
2. Define the scope
Decide whether your audits will be general or targeted:
- General audits: Provide a comprehensive review of all safety exposures across a facility.
- Targeted audits: Focus on specific risks, such as electrical hazards or compliance with a particular OSHA standard.
Combining both approaches can strengthen your overall safety efforts. For example, a monthly facility-wide audit can identify broad risks, while a targeted inspection the following month might focus on personal protective equipment (PPE) usage.
3. Assign participants
Select individuals or teams to conduct the audits. This may include:
- Safety committees or dedicated safety teams.
- Department supervisors and managers emphasize that safety is a shared responsibility.
- Frontline employees who provide valuable insights into daily hazards.
- External experts or insurance representatives for specialized inspections.
Involving employees not only improves the quality of audits but also boosts their engagement in safety initiatives.
4. Identify inspection elements
Focus on two major areas during your audits:
- Physical hazards: Equipment, materials, tasks, and environmental conditions that could lead to injuries.
- Human factors: Training programs, written policies, safety culture, and adherence to safe work practices.
Review past injury and illness records (e.g., OSHA 300 logs) and existing inspection reports to prioritize high-risk areas.
5. Set priorities
Not all hazards can be addressed simultaneously. Use a risk assessment framework to prioritize corrective actions based on:
- Probability: How likely is the hazard to cause harm?
- Severity: How severe would the injury or illness be?
- Exposure: How many employees are at risk?
For high-risk hazards, take immediate action. Lower-risk issues can be scheduled for correction based on available resources.
6. Create an inspection schedule
Develop a schedule that includes a mix of:
- Routine checks: Daily or shift-start inspections conducted by operators.
- Periodic inspections: Weekly or monthly audits by safety committees or supervisors.
- Annual reviews: External inspections by insurance providers or specialized vendors.
Consider a combination of planned and unannounced inspections to ensure a thorough and realistic assessment of workplace conditions.
7. Develop checklists
Checklists are critical for maintaining focus and consistency during inspections. A good checklist should cover:
- Specific equipment and processes to review.
- Safety practices and procedures to observe.
- Steps to evaluate the operational condition of machinery.
Tailor checklists to your organization’s unique needs and update them as processes or regulations change.
Make safety audits work for your organization
A successful safety audit program is more than a compliance exercise—it’s a tool for fostering a culture of safety, efficiency, and continuous improvement. By systematically identifying and addressing risks, EHS leaders can reduce workplace injuries, enhance employee morale, and drive operational excellence.
When implemented effectively, safety audits provide actionable insights, strengthen employee trust in safety protocols, and position your organization as a leader in workplace safety. Don’t wait for accidents to happen; make safety audits a central pillar of your EHS strategy.
Bottom line
Safety and health audits are an essential part of any proactive safety program. By leveraging these seven strategies, you can build an audit process that delivers tangible results, ensures compliance, and fosters a safer work environment. The best safety programs aren’t reactive but proactive. As an EHS leader, your commitment to regular safety audits can set the standard for excellence in workplace safety.