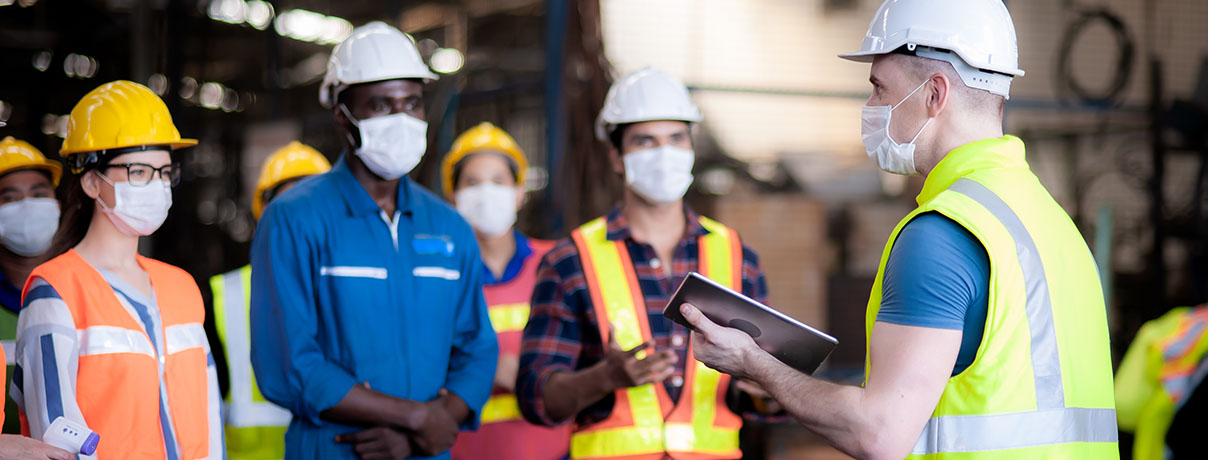
Why you should have safety meetings training
Running OSHA safety meetings time after time can lose some of the spark as an effective training tool. We’ve all been to safety meetings that missed the mark—topics were not pertinent, sessions ran too long, disorganization ruled—and we’ve seen safety training forgotten as soon as the meeting was over.
How can we avoid safety meetings that aren’t effective? What can we do to get the most effective training for the time, energy, and dollars spent in safety training?
We talked with directors of safety programs at large and small companies that have been awarded OSHA “Star” status for their outstanding safety and health achievements, and several successful tactics for running safety meetings emerged.
Successful tactics for running safety meetings
- Carefully time the length of meetings. If you hold meetings once a month, keep the length at 30-45 minutes; once a week, keep them 30 minutes or less with 20 minutes as the ideal length. The longest meetings should run no more than an hour.
- For construction work, have short, informal tailgate safety meetings of 5, 10, or 15 minutes before work once a week, with a longer talk at least once a month or at the start of each phase of the construction project.
- Schedule topics over a long period—a year is most common. The schedule provides reasonable deadlines for the trainer and helps others plan their working days.
- Select meeting topics based on 1) a review of the most recent types of accidents and near-accidents, 2) related corporate safety goals, 3) any subjects that need to be covered from a legal or insurance standpoint, and 4) your basic list of safety topics to be reviewed.
- Occasionally have the senior management person at the location open the meeting and sit in—it’s a sign of commitment.
Why are safety meetings important?
Formal employee meetings provide the best opportunity for management to spell out corporate safety goals and show support for the program. Informal training can also be helpful, he pointed out, as long as line supervisors are able to communicate safety and health concerns adequately on the job and maintain sufficient records to meet OSHA’s documentation requirements. Having a pre-planned weekly meeting is a convenient way to go over required training.