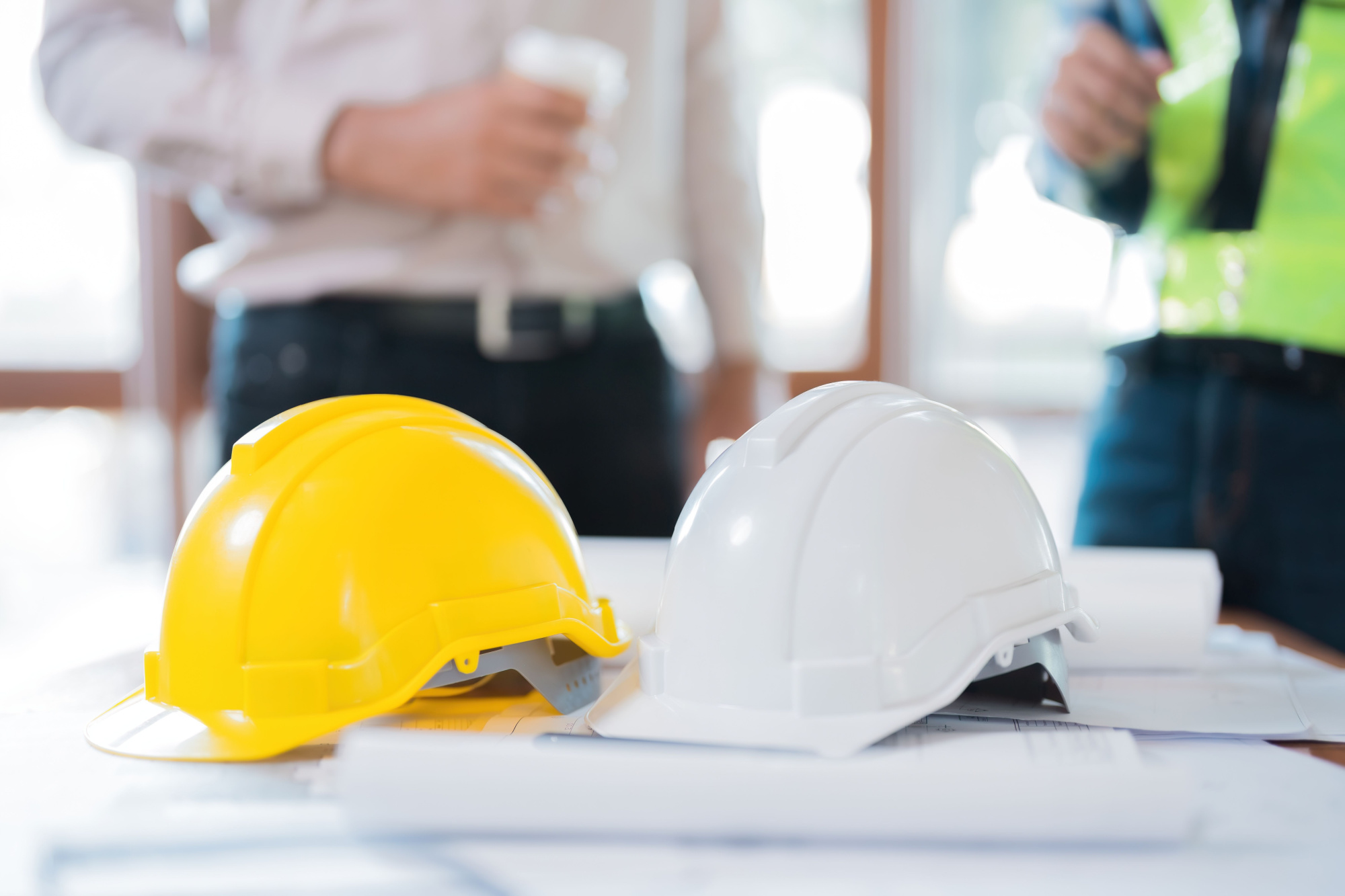
The ultimate guide to EHS management systems
Having a strong EHS management system creates a workplace that actively prevents risks, not just reacts to them. It minimizes accidents, ensures regulatory compliance, and fosters a culture of safety and awareness among employees. The positive impacts of effective EHS management extend beyond immediate safety, creating a ripple effect that enhances productivity, boosts morale, and benefits everyone involved.
However, like any new or updated system rollout, it requires careful planning and communication to avoid disruptions. Knowing what an effective EHS management system looks like can help organizations design and implement their own, leaving less room for guesswork.
In this article, we define what EHS management is, how it works, and offer tips to streamline putting the system into practice as efficiently as possible.
What is an EHS management system?
An environmental health and safety management system (EHS) is a framework companies use to make sure they’re taking the right steps to protect their workers, the environment, and overall workplace health.
It includes policies, tools, procedures and plans that help:
- Identify, assess and mitigate risks
- Prevent accidents and hazards
- Stay compliant
- Close skills gaps
- Help improve employee performance
- Promote a safe and healthy working environment
How does an EHS management system work?
Identifying and planning for risks
The first thing an organization needs to do is identify risks. This means examining operations and pinpointing potential hazards, such as dangerous machinery, chemical exposure, or environmental pollution.
Once those risks are clear, it’s all about creating a plan to tackle them. Think actionable, specific goals like reducing workplace injuries, reducing emissions, or improving how waste is managed. The idea is to get ahead of the problem before it becomes a crisis.
Assigning roles and training employees
Now that you’ve got a plan, someone needs to own it. Leadership typically assigns teams or individuals to manage health, safety, and environmental initiatives. These people perform tasks like keeping the company compliant, running audits, or communicating safety updates.
In addition to having the right people in charge, you also have to make sure everyone is on the same page. That’s where training comes in. Employees need to know the protocols, why they matter, and how their actions contribute to the bigger picture.
Using tools and technology
Companies often use software to log safety incidents, track compliance, or monitor progress toward goals. Beyond that, there are tools like air quality sensors or noise meters to keep tabs on workplace conditions in real time. This kind of data is crucial because it helps you spot issues early and fix them before they snowball into something bigger.
Implementing safety measures
This is where plans are put into action. Employees follow safety protocols, whether they wear protective gear or handle materials with extra care. Meanwhile, companies might make bigger changes, like upgrading old equipment, improving ventilation, or reworking workflows to make them safer.
Monitoring and reviewing performance
No system works perfectly without regular check-ins. Inspections, audits, and performance reviews are how you figure out if everything’s running smoothly. Are you hitting your goals? Have accidents decreased? Are employees completing the required training on time? Answering questions like these will help companies take stock of what’s working, what’s not, and where adjustments might be needed.
Making improvements over time
When goals aren’t met, companies adapt by introducing new policies, updating training programs, or investing in better tools. EHS management is a continuous process; as conditions and regulations change, your system must evolve alongside it.
Tips to implement an EHS management system
Staying on top of safety efforts can help reduce avoidable workplace injuries. The key is for safety managers to encourage and motivate their companies to adopt the same sentiment. Here are some ways to do that.
1. Stay up to date on policies and procedures
Change is a common theme for companies, whether related to technologies, employee dynamics, or regulatory changes. As these changes occur, it’s important to ensure policies and procedures align with them. If a company moves offices, for example, some of its safety guidelines may need to be changed to correspond with the new setup.
When possible, it’s also beneficial to consider future plans in the pipeline and begin brainstorming how to manage policies and procedures in those cases. Gather employee input to ensure policies remain relevant to day-to-day operations and communicate updates clearly to the entire organization.
2. Serve up safety training in small doses
Long, one-size-fits-all training sessions often lead to disengagement. Instead, break training into smaller, role-specific sessions focusing on practical, actionable knowledge. For example, forklift operators might focus on handling-specific hazards, while office staff learn ergonomic best practices.
Use tools like short videos, quizzes, or microlearning platforms to deliver training in an engaging way that employees can retain and apply immediately. You can also schedule routine emergency preparedness drills to ensure employees know how to handle emergencies properly.
3. Monitor employees and workplace practices
While additional training can help reinforce safety measures, it’s important to see firsthand that employees are observing such guidelines. For instance, safety managers should regularly check to see if employees are using the safety equipment and tools made available to them.
Employees should also ensure that the equipment fits and works correctly. If anything doesn’t meet the required guidelines, employees should take steps to fix the issue.
Monitoring workplace safety often feels like walking a fine line between oversight and micromanagement. The key is normalizing regular observations as part of a collaborative safety effort. Use checklists or workplace audits to ensure consistency and adopt tools like sensors or safety apps for real-time data collection. Train supervisors to provide constructive feedback during monitoring to address risks and reinforce safe practices without creating distrust.
4. Create a culture of open communication
Open communication is vital for uncovering safety risks and building trust. Employees should feel free to speak up about safety and health concerns in the workplace and suggest ideas for improvement. One way to facilitate this is by holding meetings during which employees can share their constructive feedback.
You can also create an online portal or set up a hotline service where employees can report issues anonymously. These efforts offer greater insight into issues that may not have been apparent beforehand. Share updates on resolved issues to show that employee input leads to meaningful improvements.
Make sure that when you make the first big step to open communications, your organization is truly ready to listen and act. This can backfire on you and make relationships with personnel worse, particularly if they put out the effort to share their knowledge and energy and saw no action. On the other hand, meaningful action taken against issues can improve relationships with personnel dramatically.
5. Adopt a centralized system to track EHS data
Fragmented data can lead to missed deadlines, compliance gaps, and inefficiencies. Using a centralized system creates one reliable place to track the incident types important to your company, monitor training progress, and measure compliance.
Choose a user-friendly platform that integrates with existing workflows and provides real-time insights. Train employees on the system and emphasize its role in reducing the administrative burden and improving decision-making.
6. Set clear EHS objectives and goals
Without clear goals, it’s hard to measure success or maintain focus. Use baseline assessments to set SMART goals (specific, measurable, achievable, relevant, and time-bound) that align with organizational priorities.
For example, aim to reduce incident rates by 10% in a year or complete 100% of safety training by a specific date. Share these goals across teams and track progress with regular check-ins to keep everyone aligned.
7. Use KPIs to evaluate and improve
Having metrics to benchmark the performance of your EHS management system makes it a lot easier to accurately identify areas for improvement. Here are some key performance indicators (KPIs) to keep in mind while you’re evaluating:
- Incident rate: Track the number of workplace accidents or safety incidents over a specific period.
- Near-miss reports: Monitor the frequency of potential accidents that were avoided to highlight proactive hazard identification.
- Compliance score: Measure adherence to health, safety, and environmental regulations during inspections or audits.
- Training completion rate: Assess the percentage of employees who have completed required safety or compliance training.
- Lost time injury rate (LTIR): Monitor the injuries resulting in time away from work per 100 full-time employees annually.
- Employee feedback: Gather input on safety practices or workplace conditions through surveys to identify areas for improvement.
- Corrective action closure rate: Track how quickly identified issues or risks are resolved after they’re reported.
8. Reward safe practices
Even the most well-thought-out processes can be ineffective if employees aren’t engaged. Positive reinforcement can be a powerful tool to combat this, providing motivation to stay on track. Consider rewarding safe practices with incentives like gift cards, public recognition, or buying the team lunch when quarterly safety goals are met. Giving employees a common goal helps create a shared sense of responsibility, creating an environment where everyone is invested in achieving a common goal.
Simplify your EHS tech stack
Efficiently managing your EHS program requires an integrated approach that leverages workflow automation, standardizes processes, and empowers users at every level. Our EHS management system, EHS Hero is a uniquely scalable, unified solution that maximizes employee safety and the return on your EHS technology investment.
EHS Hero’s compliance insights are provided by a team of in-house EHS industry experts across 197 subject areas. Their expertise is leveraged to build plans, checklists, guidance documents, and instructor-led teaching materials, as well as easy-to-understand summaries of federal and state regulations. With tools designed by former EHS professionals, ensuring a unique blend of features and capabilities that are easy to use and talk to one another. This makes it simple for EHS professionals to start and complete tasks in one interface.
Ready to upgrade your EHS management system? Contact us today to see how BLR can help you move the needle in your organization.