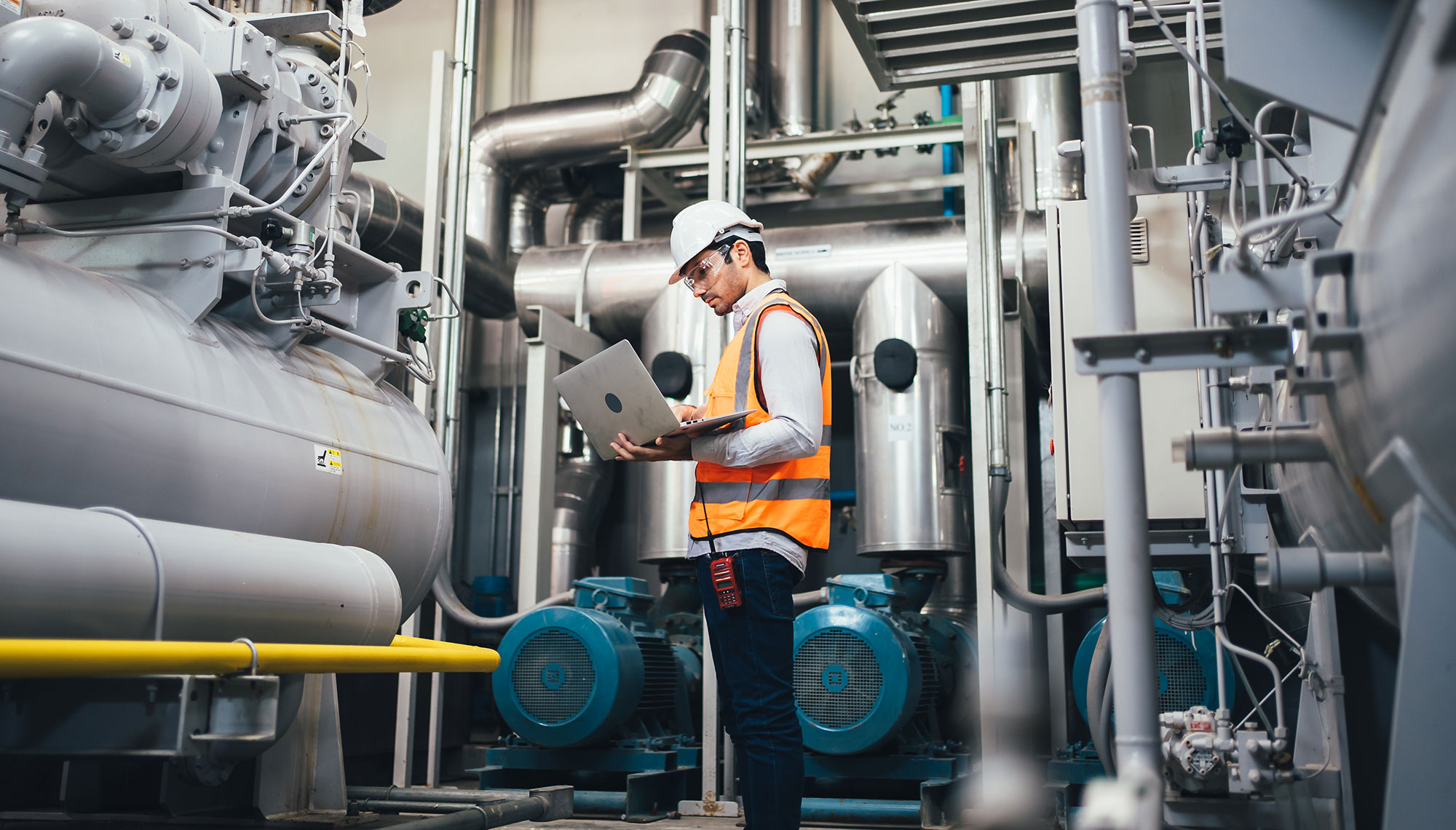
The 14 elements you should include in your PSM program
Keep your PSM program up to speed: 14 OSHA requirements
The Occupational Safety and Health Administration (OSHA) created the first PSM requirements in 1992 in response to a series of catastrophic incidents related to highly hazardous chemicals (HHC). These requirements have been updated and expanded several times in the last two decades, and all HHC-related companies should keep a lookout as they operate and expand.
Despite the PSM regulations, numerous fatalities and catastrophic process-related incidents prompted OSHA to establish a PSM Covered Chemical Facilities National Emphasis Program (PSM NEP), which targets PSM facilities for OSHA inspections. As a result, OSHA enforcement of the PSM standards is very active, often resulting in six-figure fines.
What are the PSM requirements?
To make sure your company is compliant, keep in mind the following 14 elements that OSHA inspectors will look for when they review your PSM program.
1. Employee participation
Perhaps one of the most important mandates, the employee participation clause requires that employees—including production and maintenance staff—be involved in every aspect of the PSM programs at their respective worksites. They must also be represented at the meetings where PSM-related issues are discussed. OSHA requires employee participation to be followed as written, so employers should create formal plans.
2. Process safety information
According to OSHA’s PSM mandates, “The employer shall complete a compilation of written process safety information before conducting any process safety hazard analysis required by the standard.” In other words, all workers should be able to access and understand the technical data regarding the HHC-related risks they face on the job.
3. Process hazard analysis
One of the most technical elements of PSM, Process Hazard Analysis requires that engineers and maintenance leaders analyze the consequences of safety failures. These analyses must be conducted in teams, and OSHA requires that each team must include one person who is “knowledgeable in the specific process hazard methodology being used.”
4. Operating procedures
Plenty of potential chemical hazards follow turnarounds and emergency shutdowns. OSHA inspectors want to see that companies have plans for keeping everyone safe as they start back up. This includes having clear and detailed operating procedures in place for all aspects of the process, from start-up to shut down. These procedures should be easily accessible to all employees and regularly reviewed and updated to ensure they are effective in preventing accidents and injuries.
By following these guidelines and ensuring that all workers are properly trained and informed, companies can create a safer work environment and reduce the risk of hazardous incidents. It is essential for companies to prioritize the safety of their employees and comply with all regulations to prevent accidents and protect the well-being of their workforce.
5. Training
Workers who carry out processes involving highly hazardous chemicals need to be well-trained, and their training should have been accomplished through a competent source, first-party or otherwise. OSHA requires that their training be well-documented. Training management software makes it much easier to track this.
6. Contractors
Regular employees and contractors alike must be well informed of the hazards they face. Under the PSM National Emphasis Program (PSM-NEP), “The employer shall inform contract employers of the known potential fire, explosion or toxic release hazards related to the contractor’s work and the process.”
7. Pre-startup safety review
Are you reviewing your safety procedures every time a worksite starts back up? You should be. OSHA expects employers to perform pre-startup safety reviews for both new and modified facilities. This rule applies even if the procedural changes only affect a single component or process.
8. Mechanical integrity
Periodic, documented inspections are required for several systems, including:
- Pressure vessels
- Storage tanks
- Piping systems
- Ventilation systems
The employers or contractors conducting these inspections must not only be officially trained, their testing procedures must follow “recognized and generally accepted good engineering practices,” according to OSHA. In other words, your company must be able to explain WHY your inspectors made their decisions.
9. Hot work permit
Every employer needs to issue permits to employees and contractors who weld or perform other high-temperature work near covered processes. They also need to train their personnel to post and file these permits when necessary.
10. Management of change
Companies need standard procedures for managing changes to process chemicals, technology, equipment and procedures. Each change also requires the following considerations:
- The technical basis for the change.
- The impact of the change on worker safety and health.
- Necessary modifications to operating procedures.
- The necessary time period for the change.
- Authorization requirements for the proposed change
11. Incident investigation
OSHA’s state standard calls for investigations for all incidents that result in—or could have resulted in—a catastrophic highly hazardous chemical release. Because of that ambiguous wording, cautious companies must keep every potential HHC-related scenario in mind.
12. Emergency planning and response
Even minor chemical releases can lead to major incidents. This element mandates employers to create emergency plans for handling smaller HHC releases.
13. Compliance audits
According to the PSM-NEP, “Employers shall certify that they have evaluated compliance with the provisions of this section at least every three years to verify that the procedures and practices developed under the standard are adequate and are being followed.” This element also requires employers to retain at least their two most recent audit reports.
14. Trade secrets
Until recently, some companies attempted to protect proprietary information by keeping process details from their employees. To prevent this scenario and enhance worker safety, the “trade secrets” element gives employees the right to know processes that may affect their health and safety.
Process Safety Management programs are essential for managing all types of chemical operations and operations involving hazardous material. These 14 elements will make your program compliant, but having a great program requires going beyond compliance to not only protect workers and the environment but also add value to a company’s management system.