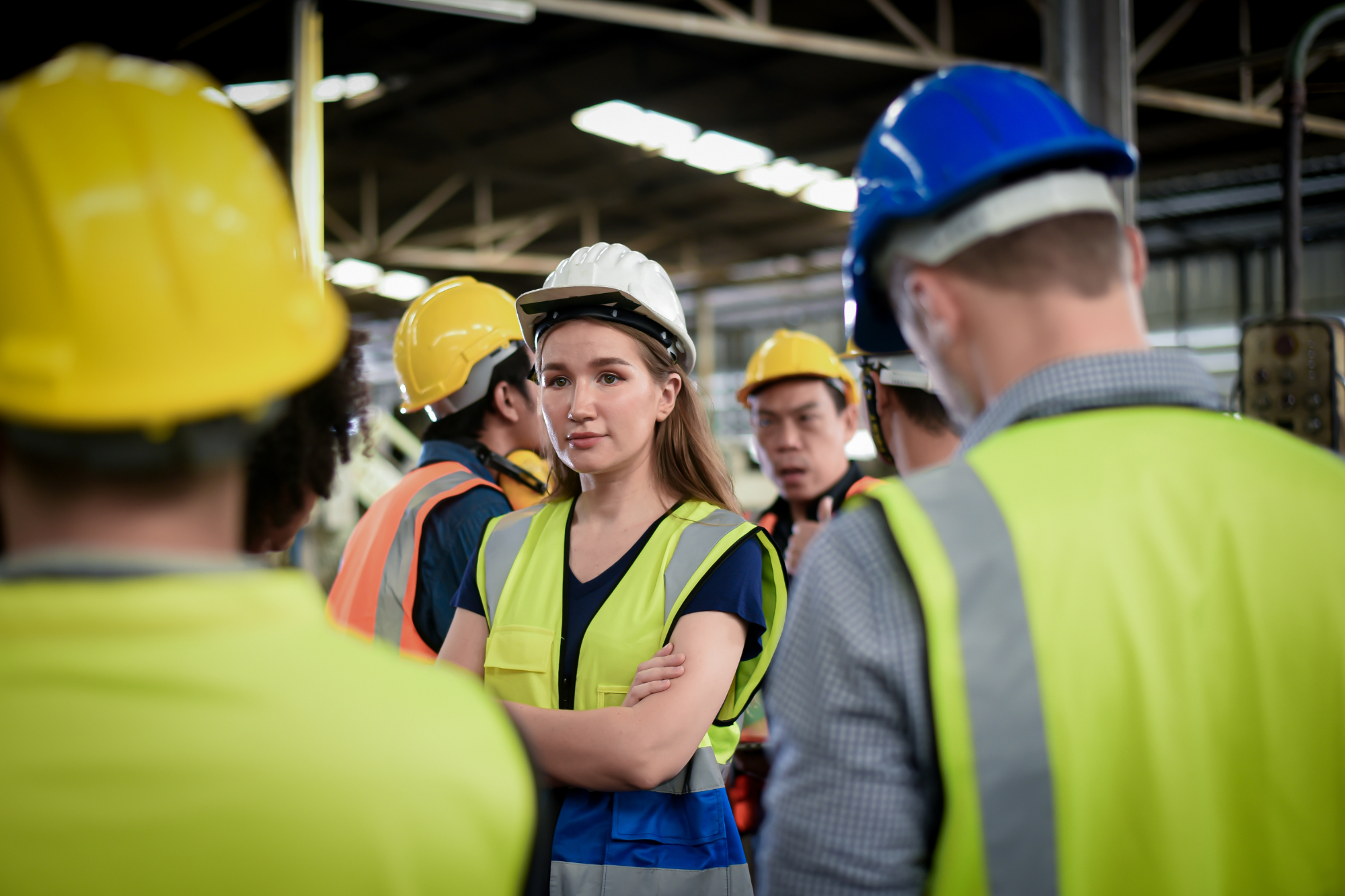
Navigating mandatory EHS training requirements
Meeting EPA, OSHA, and DOT mandatory training requirements
Many federal EPA, DOT, and OSHA employee training requirements direct employers to inform, educate, and train employees to protect themselves, the public, or the environment from workplace hazards. Some of these requirements are highly prescriptive, outlining detailed steps for certification, including specific coursework, testing, or hands-on demonstrations. These structured training programs ensure that employees gain the necessary technical knowledge and skills to perform their jobs safely and in compliance with regulations.
However, most training requirements are “performance-based,” meaning they focus on qualitative goals such as “effective,” “lead to understanding,” or “demonstrate proficiency” rather than dictating a specific training format. This flexibility allows employers to tailor training programs to their workforce’s unique needs, industry risks, and operational constraints. This also places the responsibility on employers to ensure that training methods effectively achieve the intended outcomes, which can be challenging without clear regulatory benchmarks.
OSHA training
The Occupational Safety and Health Administration’s (OSHA) goal for safety training is the long-term reduction of injuries and illnesses among workers. OSHA safety training is designed to help workers identify hazards, prevent injuries, and ensure proper safety protocols are followed in the workplace. To assess effectiveness, OSHA evaluates training at both immediate and long-term levels.
Immediate effectiveness is measured through
- Workplace inspections
- Test scores and written assessments
- Employee surveys
- Observation of workers performing tasks
Long-term effectiveness is assessed by tracking
- Worker attitudes toward risk reduction and hazard control
- Changes in work practices among trained employees over time
- Trends in reported health and injury rates
By focusing on both short- and long-term outcomes, OSHA training requirements ensure that safety training not only imparts knowledge but also leads to sustained improvements in workplace safety.
EPA training
The Environmental Protection Agency (EPA) establishes training requirements primarily to prevent pollution and reduce the release of hazardous substances into the environment. While the agency prioritizes compliance with environmental standards, it typically grants employers flexibility in determining how EPA training is conducted, as long as employees gain the necessary knowledge to comply with regulations and perform their duties safely.
Some EPA regulations require more structured training and certification processes, particularly for industries handling hazardous or toxic materials. For example:
- Asbestos and lead abatement. Workers involved in removing asbestos or lead-based paint must complete specialized training and obtain certification to ensure proper handling, removal, and disposal in accordance with EPA guidelines.
- Hazardous waste management. Employees responsible for handling, storing, or disposing of hazardous waste must be trained under the Resource Conservation and Recovery Act (RCRA) to prevent spills, contamination, and regulatory violations.
- Pesticide application. Individuals applying restricted-use pesticides must complete EPA-approved training and certification to minimize environmental impact and public health risks.
Employers must ensure that workers receive comprehensive training that meets both environmental and workplace safety standards to avoid regulatory penalties and mitigate risks to employees, the public, and the environment.
DOT Hazardous Materials training
The Department of Transportation (DOT) requires all employees who handle, transport, or prepare hazardous materials for shipment to receive specialized training to ensure the safe movement of these materials and compliance with the Hazardous Materials Regulations (HMR). DOT training requirements apply to various roles, including warehouse workers, drivers, shipping personnel, and emergency responders.
Hazmat employers are responsible for ensuring that their employees receive proper training, pass competency assessments, and obtain certification. Employers must also maintain up-to-date records of all completed training.
Required hazmat training includes:
- General awareness and familiarization: Provides employees with a broad understanding of hazardous materials regulations.
- Function-specific training: Focuses on the particular tasks an employee performs in relation to hazardous materials.
- Safety training: Covers procedures to protect employees, the public, and the environment from potential hazards.
- Security awareness training: Educates employees on identifying and responding to security risks.
- In-depth security training: Required for employees working with high-risk hazardous materials and when a security plan is mandated.
- Driver training: Necessary for any hazmat employee responsible for transporting hazardous materials.
Overlapping training requirements
While EPA, OSHA, and DOT each enforce distinct training requirements, there is often overlap among them. For instance, employees responsible for hazardous waste management may also be involved in preparing hazardous materials for transport. In such cases, multiple training requirements apply, including EPA hazardous waste training, OSHA HAZWOPER regulations, and DOT hazardous materials handling standards.
Additionally, OSHA and EPA may impose separate training requirements for the same operation, process, or substance. This can create challenges for employers in determining which regulations take precedence or how to ensure compliance with multiple standards. A thorough understanding of each agency’s requirements is essential to developing a strong EHS safety training program that meets all applicable regulations.
5 best practices for effective EHS training compliance
Meeting EPA, OSHA, and DOT training requirements is a process that requires careful planning and regular updates. To ensure compliance, employers should consider the following best practices:
- Conduct regular training assessments. Periodically review EHS training programs to ensure that training aligns with current regulations and industry standards.
- Keep thorough records. Maintain detailed documentation of employee training, including completion dates, certifications, and refresher courses, to demonstrate compliance during inspections.
- Use multiple training methods. Combine training methods such as online learning, in-person instruction, hands-on training, and safety drills to reinforce key concepts and improve retention.
- Schedule refresher training. Many regulations require periodic retraining. Establish a schedule to keep employees up to date on new policies and procedures.
- Integrate compliance training with workplace safety culture. Encourage employees to view training as part of a broader commitment to workplace safety and environmental responsibility rather than just a regulatory obligation.
Take a proactive approach to EHS compliance
Achieving success and avoiding significant fines requires organizations to be proactive in managing EHS compliance with both state and federal regulations.
With BLR’s EHS Hero and TrainingToday, you can access comprehensive training materials from instructor led presentations to self-paced online training courses and efficiently track regulatory training requirements including training frequency, inclusions and instructor qualifications.
BLR’s comprehensive training management, centralized record-keeping and intuitive workflow tools are backed by a team of industry experts with over a century of combined experience. They provide the guidance and resources organizations need to stay compliant with the latest regulatory changes from EPA, OSHA, and DOT, ensuring the protection of both employees and the environment.