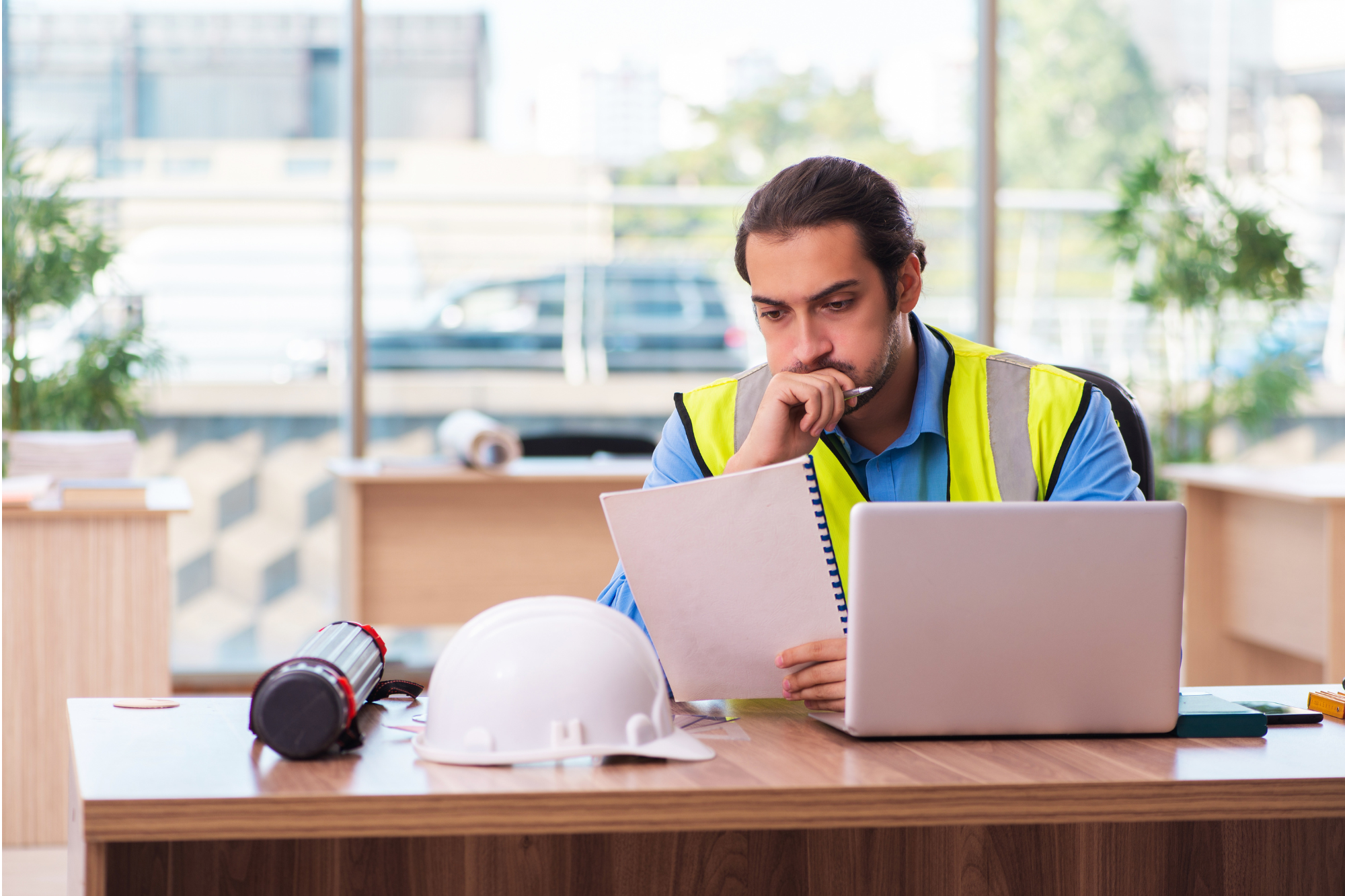
How to prevent workplace accidents with job hazard analysis
Have you ever heard the saying, “an ounce of prevention is worth a pound of cure?” This adage holds particularly true in workplace safety. Preventing accidents and injuries before they occur is far more effective and cost-efficient than dealing with the aftermath. Fortunately, there is a powerful tool that helps achieve this proactive approach: the Job Hazard Analysis (JHA).
According to the Occupational Safety and Health Administration (OSHA), a Job Hazard Analysis (JHA) is a technique that focuses on the relationship between the worker, the task, the tools, and the work environment. By identifying uncontrolled hazards within this relationship, employers and workers can take steps to eliminate or control them, significantly reducing the risk of injuries and accidents.
While the idea of completing additional paperwork may not seem appealing, the benefits of a well-executed JHA far outweigh the effort involved. A JHA is not just another administrative burden; it is an invaluable safety measure that can save lives and protect livelihoods. Workers, as the individuals closest to the tasks, are uniquely positioned to identify hidden hazards and inadequacies in controls. Their firsthand experience provides critical insights that make JHAs highly effective.
Although performing JHAs for every task in your workplace may seem like a daunting undertaking, the long-term advantages are undeniable. Businesses that invest time and resources into JHAs reap rewards such as reduced workers’ compensation costs, decreased downtime, lower turnover rates, and improved productivity. Perhaps most importantly, employees will recognize that their employer values their well-being enough to make safety a priority. This fosters a culture of trust, loyalty, and accountability.
How to create a JHA
Creating a Job Hazard Analysis is a straightforward but detailed process. By following these steps, you can systematically address workplace risks and build a safer work environment.
Step 1: Prioritize your tasks
The first step in creating a JHA is to prioritize tasks. Begin by engaging with your workers to identify all tasks performed as part of your operation. Workers are often aware of risks that may not be immediately obvious to supervisors. Additionally, review near-miss reports and injury and illness records. These documents can highlight tasks that pose significant hazards.
If you identify tasks involving immediate dangers to life or health, take immediate action to control those hazards. These high-risk tasks should be addressed before performing a full JHA to ensure the safety of everyone involved.
Step 2: Assess your tasks
Once you have a comprehensive list of tasks, rank them by their level of risk. Consider two key factors: probability and severity.
Probability refers to the likelihood of an injury or illness occurring, ranging from “no chance” to “almost certain.”
Severity measures the potential outcome, from minor injuries to multiple fatalities.
Tasks with a high probability of occurrence and severe potential outcomes should be analyzed first. This prioritization ensures that the most dangerous jobs are addressed promptly.
Step 3: Break down your jobs
Breaking down jobs into individual steps is the core of a JHA. This process involves careful observation, consultation, and analysis. Here’s how to approach it:
Observe and document job steps
Watch workers perform the job and note each step required to complete it. Aim for a level of detail that thoroughly describes the process without becoming overly granular. For example, instead of stating, “use a wrench to tighten the bolt,” break it down into steps like “pick up the wrench,” “position the wrench on the bolt,” and “tighten the bolt.” While this may seem tedious, it ensures that no critical step is overlooked.
Collaborate with multiple workers and supervisors to gain diverse perspectives. Different individuals may notice hazards or nuances that others miss.
Identify hazards
For each step, consider the potential hazards. Ask questions such as:
- How could an injury occur during this step?
- What is the likelihood of this injury happening?
- What are the possible consequences?
- Are there any contributing factors that could increase the risk?
This thorough examination ensures that even less obvious risks are identified.
Establish hazard controls
After identifying hazards, determine controls to eliminate or reduce them. Controls can include:
- Engineering controls (e.g., machine guards, improved ventilation)
- Administrative controls (e.g., training, job rotation)
- Personal protective equipment (PPE) (e.g., gloves, goggles)
For instance, if a step involves lifting heavy objects, the hazard could be the risk of a back injury. Controls might include providing proper lifting equipment, implementing a two-person lift policy, and offering ergonomic training.
Consider an example: changing a car tire. A step might involve jacking up the car. The associated hazard is the car slipping off the jack, potentially crushing someone. Controls would include setting the parking brake, chocking the tires, and using jack stands to secure the vehicle.
Step 4: Review and update
A JHA is not a static document; it requires regular review and updates. As workers find more efficient ways to complete tasks or as new tools and methods are introduced, the dynamics of a job can change. These changes, while often intended to improve productivity, can inadvertently increase risks.
Periodic reviews ensure that JHAs remain accurate and relevant. When reviewing a JHA, observe current practices to confirm they align with the documented steps and controls. If deviations are found, assess whether they make the task more hazardous or if they represent a safer alternative. Never accept changes that compromise safety, and always involve workers in discussions about updates to reinforce their role in maintaining a safe workplace.
Benefits of Implementing JHAs
The effort put into creating and maintaining JHAs pays off in multiple ways:
Enhanced safety
By identifying and controlling hazards, JHAs significantly reduce the likelihood of workplace injuries and illnesses.
Cost savings
Preventing accidents leads to lower workers’ compensation claims, reduced medical expenses, and fewer fines from regulatory agencies.
Increased productivity
A safe work environment minimizes disruptions caused by accidents, allowing employees to focus on their tasks without fear or distraction.
Improved morale
Workers who feel that their safety is a priority are more likely to be engaged, loyal, and satisfied with their jobs.
Compliance with regulations
Adhering to OSHA guidelines and other safety standards helps businesses avoid legal issues and demonstrates a commitment to ethical practices.
Key JHA takeaways
An ounce of prevention is indeed worth a pound of cure, and nowhere is this more evident than in workplace safety. The Job Hazard Analysis is a powerful tool that helps businesses identify and address risks before they result in harm. While the process requires time, effort, and collaboration, the rewards—a safer workplace, reduced costs, and increased employee trust—are well worth it.
By prioritizing tasks, systematically assessing risks, involving workers in the process, and regularly reviewing JHAs, employers can create an environment where safety is not just a policy but a culture. In doing so, they protect their most valuable assets: their people.