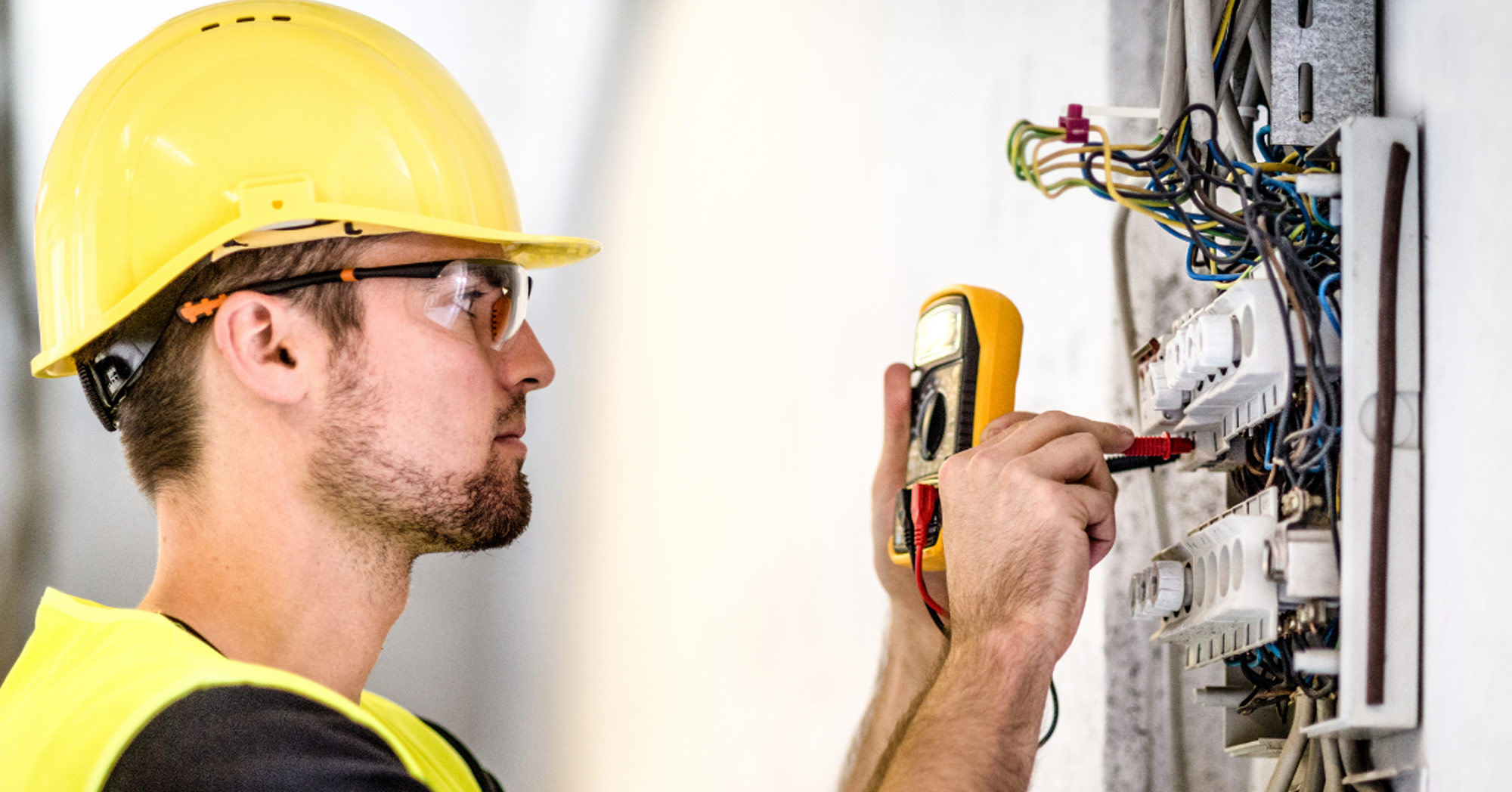
Common electrical hazards: How to identify and prevent them
Electrical equipment is a common sight in nearly all workplaces. People who work either directly or indirectly with electricity are often exposed to electrical hazards. Most electrical hazards can be avoided with a proper understanding of electrical equipment and by following some simple precautions. Described below are some of the most common electrical risks.
Overhead power lines
Overhead power lines are one of the most common workplace electrical hazards. They carry high voltages and can cause severe electrical shock and burns. According to the U.S. Occupational Safety and Health Administration (OSHA), contact with overhead power lines is responsible for nearly 50% of all electrical fatalities in the workplace each year.
It’s essential to maintain a minimum distance of 10 feet from overhead power lines at all times. This applies not only to workers but also to any equipment in use. Before starting work, install safety barriers and clearly visible warning signs to alert personnel of the hazard. Additionally, conduct regular site inspections to ensure that no materials or tools are stored beneath power lines, minimizing the risk of accidental contact.
Faulty or damaged electrical equipment
Often times, people tend to ignore faulty or damaged electrical equipment or tools used to handle such equipment. This can prove to be fatal. Always inspect all the tools and equipment for cracks, cuts, or abrasions before use. Cables, cords, wires, and other electrical components should not have any type of fraying or defects. Insulation must be intact. If any tools or equipment are faulty or damaged, they should be immediately removed from service until they can be repaired or replaced. Electrical tape is not suitable for repairing damaged insulation on electrical tools and equipment. Lockout/Tagout (LOTO) procedures should always be initiated prior to performing repairs and maintenance on electrical equipment. These procedures are designed to safeguard people working with electrical equipment by keeping the equipment de-energized.
Overloaded circuits and improper wiring
Improper wiring and overloaded circuits are major fire hazards, often leading to equipment overheating and fires. To prevent these risks, only use electrical equipment that you are properly trained and qualified to operate. When using extension cords or power strips, ensure they are rated for the equipment you’re connecting and never overload them by plugging in too many devices.
Overloading can cause excessive electrical flow, increasing the risk of a fire. Ensure that wiring is upgraded to meet the demands of your equipment and avoid overloading outlets. Always use appropriate circuit breakers for added protection. Regular fire safety audits are essential to identify and address potential issues with faulty wiring or overburdened circuits.
Lack of grounding
Grounding is key when working with electrical equipment, cables, and conductors. It prevents electricity from coming into contact with you and making you part of an electrical circuit. Improper grounding is a frequent and dangerous mistake in many workplaces. According to the National Safety Council, electrical shock caused by improper grounding accounts for approximately 30% of all electrical fatalities in the workplace each year.
To reduce the risk of electrical shock, all portable electrical equipment and tools must be either properly grounded or double-insulated. Always inspect the cords you use to ensure they have an intact grounding prong, and check that it isn’t damaged. Double-insulated tools will be clearly marked by the manufacturer with a label or tag. When electrical equipment isn’t correctly grounded or insulated, the risk of electrical shock, burns, or even electrocution increases significantly. Regularly checking for proper grounding is a simple but critical step in ensuring worker safety.
Wet or damp environments
Water and electricity are a dangerous combination. Since water is an excellent conductor of electricity, wet environments significantly increase the risk of electrical shock, especially if equipment has damaged insulation. Never operate electrical equipment in wet conditions, and always ensure your hands are completely dry before plugging in, unplugging, or handling any electrical devices. Keep work areas dry, organized, and free from water or moisture whenever possible. If electrical equipment does become wet, do not touch it. Instead, consult a qualified electrician before attempting to use or inspect it. Taking these precautions is crucial to avoiding electrical accidents in damp environments.
Arc flash and arc blast
An arc flash is a sudden release of energy caused by an electrical fault that can create intense heat, light, and pressure waves. It occurs when an electrical current jumps from one conductor to another, creating a flash of electricity that can reach temperatures of up to 35,000°F. The intense heat can cause severe burns, while the explosion can lead to hearing loss, eye injuries, or even death. Arc blasts, which result from a similar fault, can cause a violent explosion, further increasing the risk of injury or death.
To mitigate the risks of arc flash and arc blast, employers should implement proper maintenance schedules for electrical systems and ensure that workers are trained in identifying and responding to potential arc flash hazards. Personal protective equipment (PPE), including flame-resistant clothing, face shields, and insulated tools, should be worn by anyone working with or near live electrical equipment.
Proactive electrical safety measures for a safer workplace
Electrical hazards in the workplace present significant risks, but with the right precautions, training, and safety protocols, many of these dangers can be effectively mitigated. One of the most effective ways to reduce electrical injuries is by conducting regular, thorough site inspections with the help of a qualified electrical professional. In addition, employers should implement key safety measures such as installing safety barriers, machine guards, and enforcing Lockout/Tagout (LOTO) procedures to prevent accidental electrical exposure.
By routinely inspecting equipment, ensuring proper grounding, avoiding wet environments, and strictly following LOTO protocols, employers can greatly reduce the risk of electrical accidents. A proactive safety approach—where employees are properly trained, equipped with the necessary protective gear, and fully aware of potential electrical hazards—creates a culture of safety and responsibility. With these safeguards in place, electrical injuries and fatalities can be significantly reduced, leading to a safer, more efficient workplace for everyone.