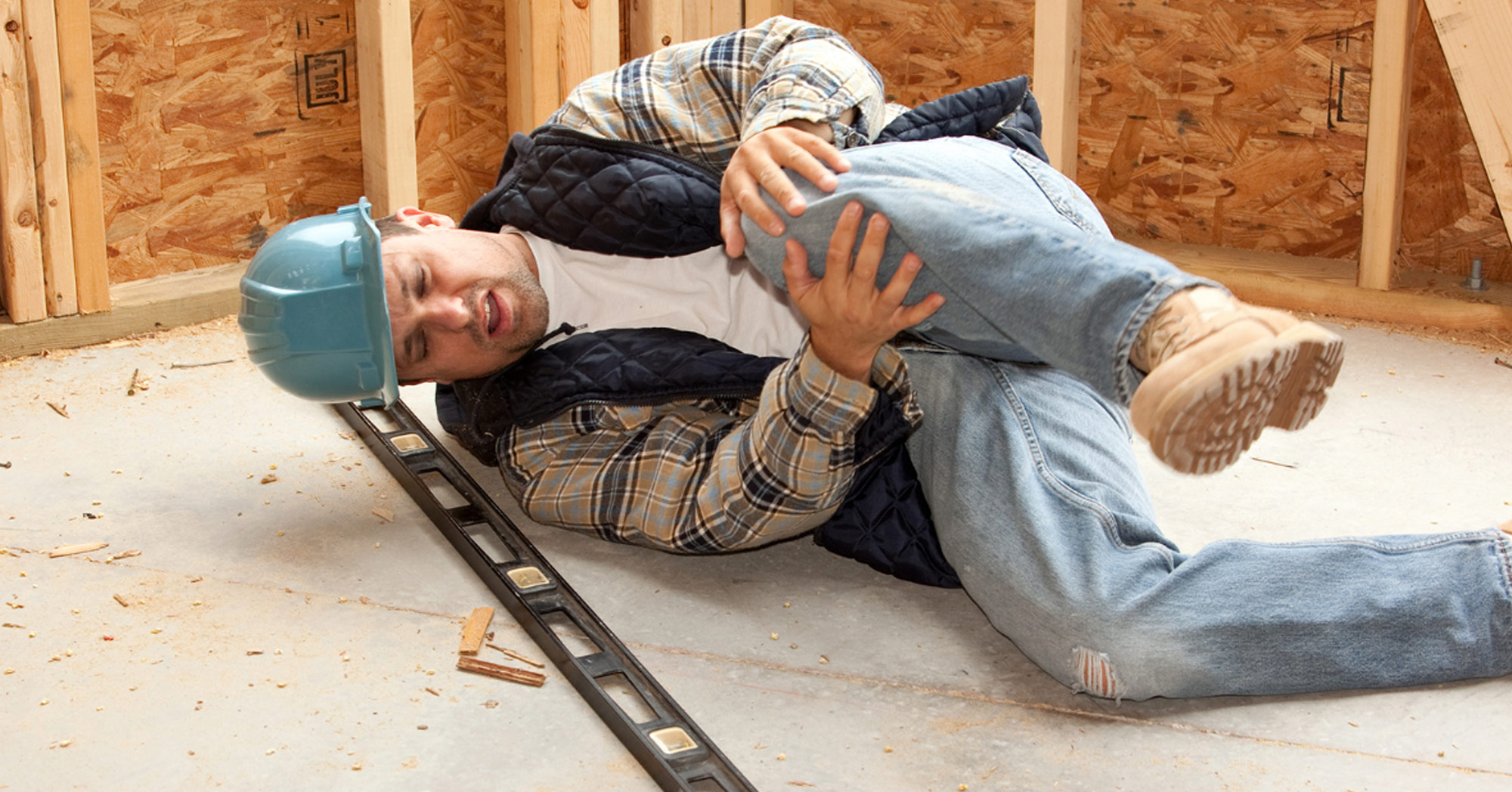
7 preventable causes of workplace injuries
When workplace injuries occur, it’s natural to look to equipment failures or unsafe conditions as the culprit; however, this is not always the case. Often, workplace injuries happen because of preventable human actions and decisions. In fact, according to the National Safety Council, 90% of employers say that tired employees have a harmful impact on their workplace.
Safety leaders know that most incidents aren’t caused by catastrophic failures—they’re the result of everyday decisions and conditions. Understanding these causes helps supervisors, safety coordinators, and frontline managers create safer environments by shaping habits, reinforcing procedures, and reducing risk before injuries occur. In this article, we’ll explore seven of the most common and preventable causes of workplace injuries, along with strategies to help your team mitigate these risks.
1. Complacency
While no worker anticipates an injury, overconfidence and routine can reduce vigilance, especially in familiar tasks. However, the mentality of thinking “it won’t happen to me” can be a cause for workplace accidents and injuries, and this is what would be identified as complacency.
Here are a few tips to help prevent your employees from falling victim to this:
- Reframe routine tasks as critical operations. Remind employees that no job is “simple” when safety is involved, whether it’s climbing a ladder or performing equipment inspections.
- Connect safety to personal accountability. Encourage employees to reflect on who is counting on them to return home safely each day. A simple exercise, such as writing down the names of four people relying on them to stay safe, helps make the importance of safety personal and powerful.
- Launch a “Zero incident” commitment. Introduce a “Target Zero” initiative that empowers employees to take ownership of safety outcomes. Make it a team commitment to strive for zero injuries, emphasizing a shared responsibility.
- Lead with visible, consistent reinforcement. Supervisors and leaders should model alertness and prioritize discussions around safe behaviors during daily meetings or toolbox talks. Recognition for safe practices reinforces that vigilance is an organizational value, not just a compliance requirement.
2. Frustration
Workers may experience frustration on the job for countless reasons. While it may be impossible to prepare for every factor that can contribute to a bad day, there are steps you can take to improve morale in the workplace, such as:
- Ensure equipment is functioning properly. Equipment that is breaking down or failing time and time again can cause employees to feel frustrated on the job.
- Communicate effectively with your employees. By communicating job expectations and potential hazards to your employees, you are reinforcing your commitment to their safety, leaving employees feeling valued and more confident in performing the job.
- Manage employee workload. If employees are being asked to perform more than they can safely handle in a day, they may begin to feel frustrated and rushed.
3. Worker fatigue
According to the National Institute of Health, an employee who is sleep-deprived can be just as hazardous as one under the influence of drugs or alcohol. Poor coordination, memory loss, and reduced concentration can all make a worker impaired and, therefore, more likely to be injured.
Employees know they don’t perform as well when they’re tired. Employers can implement the following to help mitigate worker fatigue:
- Remind employees to take breaks.
- Create a schedule that allows employees to rotate tasks and equipment.
- Train employees to recognize the symptoms of fatigue and know when they’re not just tired but also putting themselves at risk.
When employees can recognize the signs of fatigue, and employers instill methods to prevent fatigue from happening, they can work hand in hand to foster a safer work environment where employees are alert and ready to mitigate potential hazards.
4. Shortcut mentality
Shortcuts may seem like a way to save time, but in hazardous work environments, they create serious risks. Failing to wear personal protective equipment or bypassing established procedures all compromise safety and can lead to life-altering injuries. A shortcut mentality can also trickle into not reviewing job hazard analyses (JHAs) before beginning a new project. Employees are most successful while performing their job with discipline, precision, and a commitment to doing things the right way. Especially when lives are on the line.
Safety audits can be a helpful tool in mitigating this mentality in the workplace and identifying areas where steps are, or can be, easily skipped. They also serve as a reminder to regularly evaluate your workplace’s safety practices and programs. An effective safety program should account for our human nature. This should include multiple layers of protection, such as PPE, fall protection, and steps to properly complete the task on the job site. This helps to ensure that a single misstep doesn’t cause a worker injury or fatality.
5. Breakdowns in procedure compliance
In high-risk environments, established procedures exist for a reason: to protect lives and ensure tasks are completed safely and efficiently. Even a small deviation from a proven process can have serious consequences when working with heavy machinery, hazardous materials, or high-risk tasks.
Workers become vulnerable when systems do not reinforce the importance of each step, especially under pressure to meet deadlines or improve efficiency. To mitigate this, organizations must ensure that every task is backed by a strong, clearly communicated procedure that leaves no room for interpretation.
Leadership plays a critical role in setting this standard by regularly reviewing and updating safety protocols, reinforcing expectations through consistent training, and building systems that make compliance ingrained in every task. They must set clear expectations, enforce accountability, and empower employees to speak up when they see unsafe behaviors. Training should reinforce not just the “how” but the “why” behind each safety procedure, making it clear that every step, no matter how routine it may seem, plays a critical role in preventing injuries.
6. Lack of employee training
A common preventable cause of workplace injuries is a lack of employee training. When an organization has an established training schedule, it helps prevent injuries by educating employees on potential hazards associated with each piece of equipment at the job site.
However, effective training goes beyond a one-time orientation or a checklist of safety procedures. It requires ongoing education, hands-on practice, and reinforcement to ensure workers not only understand the risks but also know exactly how to manage them.
Investing in a comprehensive training program strengthens the entire organization. It builds confidence, sharpens skills, and empowers employees to take ownership of their safety and the safety of others.
7. Poor housekeeping
When tools, equipment, and materials are not properly stored, the risk of slips, trips, and falls increases dramatically. Cluttered walkways, wet floors, or misplaced objects can quickly turn a routine task into a dangerous incident.
Poor housekeeping also heightens the risk of fires, especially when combustible materials are allowed to accumulate in work areas instead of being stored correctly. When left unchecked, small oversights can become threats to both worker safety and operational continuity.
Establishing strong housekeeping habits is a critical part of maintaining a safe, efficient jobsite. A few ways to accomplish this include:
- Daily clean-up routines
- Clearly marked storage zones
- Regular workplace inspections
Protect your workforce by addressing preventable risks
Workplace injuries can be the consequence of preventable factors. By recognizing these risks and taking deliberate steps to address them, organizations can build a safer, stronger workforce. A proactive approach to safety not only protects individual workers but also strengthens overall operations, setting the foundation for long-term success. Empower your teams with the right training, support, and leadership, and you’ll foster a culture where safety is prioritized.