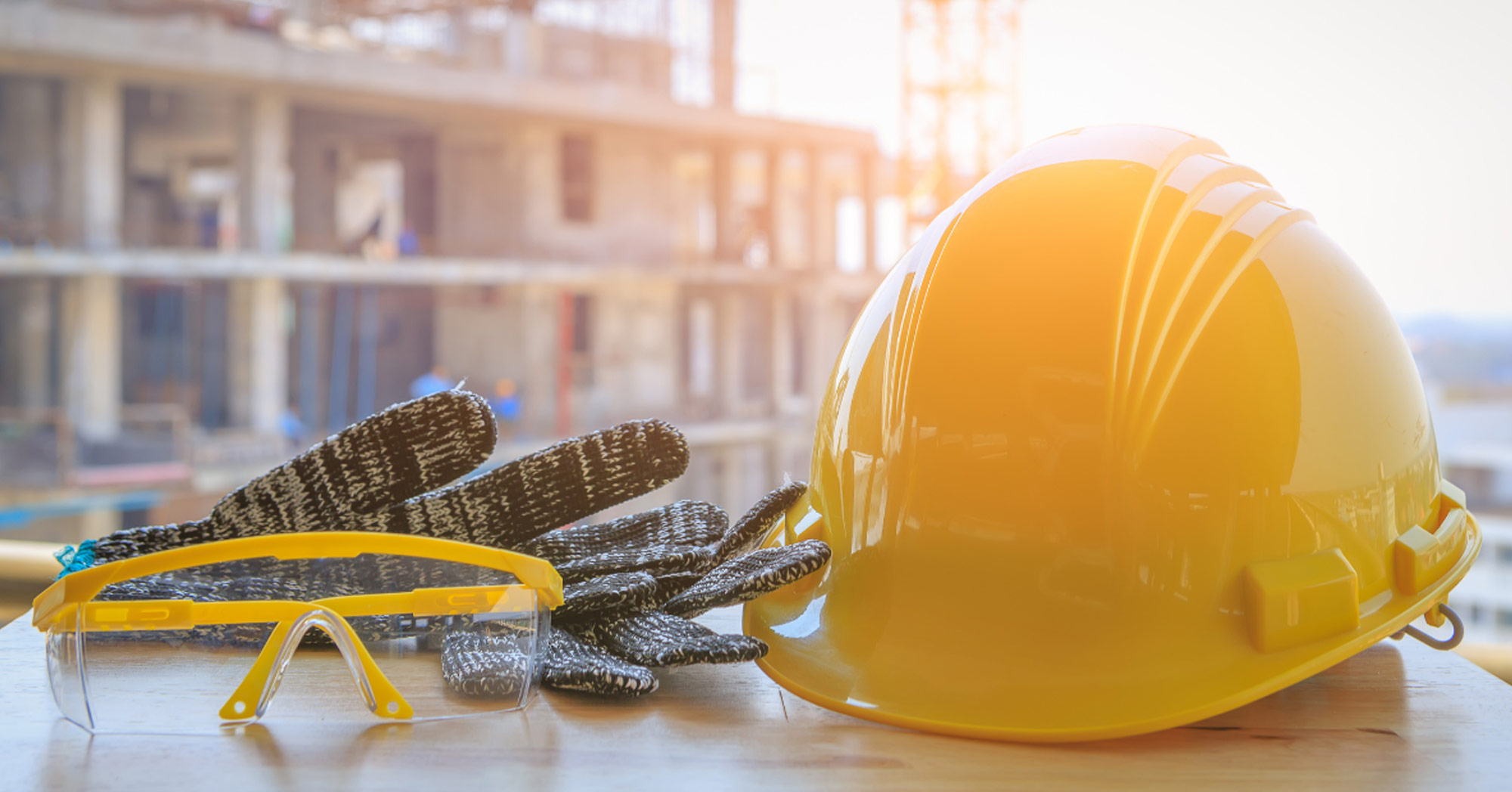
The 4 biggest safety hazards in the lumber industry
Logging remains one of the most dangerous industries in the United States. According to the BLS, logging workers have had one of the highest fatal injury rates of any occupation since 2006. And while there has been progress in improving safety conditions in the logging industry, it remains a high-risk occupation.
Four of the most significant hazards in the logging industry
- Machinery and equipment: From saws to planers, the machinery used in lumber production is powerful and can cause severe injuries. Improper use, lack of guarding, and inadequate training are common contributing factors to accidents.
- Falling objects: Logs, lumber, and other materials are constantly in motion within a lumber mill. Falling objects can strike workers, causing serious injuries or fatalities.
- Caught-in hazards: Workers can become caught in or between moving parts of machinery or trapped by logs or lumber. These hazards often lead to severe crush injuries or amputations.
- Hazardous substances: Exposure to wood dust, chemicals, and other substances can cause respiratory problems, skin irritations, and long-term health issues
The hazards carry over from the forest to the lumber yard, where employees routinely operate various types of saws and other hazardous machinery. We asked Jennifer Rudy, corporate safety manager for Swanson Group, a forest products company based in southern Oregon, about the safety hazards that keep her awake at night and how she’s addressed them in her workplace.
Forklifts
Forklifts are a common site at Swanson Group, and Rudy has good reason to be concerned about them. Forklifts or industrial trucks cause about 34,900 injuries each year in the United States alone, according to the Occupational Safety and Health Administration. OSHA requires all employees to undergo specific training before operating a forklift, and fines can be as high as $10,000 or more depending on the severity and nature of the violation.
That’s a lot of worker training to manage. A simple way to track forklift training is to store records online using a training management software. For more tips on promoting forklift safety in the workplace, check out this article.
Lockout/Tagout
In a lumber mill, there’s hazardous equipment at every turn. Machines process the logs by stripping away the bark, using round saws to cut them in half and sawmills to break them into squares. Transfer chains and kickers are also used to move the logs along, and they can also be dangerous.
Rudy realized that training workers just once on the various types of equipment wasn’t enough, so she updated her training programs to ensure that each worker is trained at every machine center annually. Swanson Group also has a color-coated and number lockout/tagout program and maintains digital records of it in the lockout/tagout tool. Employees must use the “buddy system” to review procedures for using unfamiliar equipment and receive hands-on training under supervision.
“Our policy is that they must read the job hazard analysis before they start a new job. But if you’ve never done the job, nothing replaces spending time working alongside someone with more experience.”
Slips, trips and falls
Working at heights is part of the routine for many Swanson employees. Although some have been working there 10 years or more, they frequently rotate jobs to learn new skills, Rudy said. That means on any given day, there may be several employees working in an unfamiliar area. Even seasoned veterans need reminders of the proper anchor points for their fall protection harnesses and other safety elements they may miss.
That’s why employees working in a new area are paired with a more experienced colleague and must review JHAs as they would before using new equipment.
“The buddy system takes a lot more time, but it’s worth it,” Rudy said. “We’re giving them the fair amount of time they need to learn the job.”
Personal protective equipment (PPE)
Wearing the right personal protective equipment, such as hard hats and safety goggles, is a basic responsibility of each worker. But with so many employees spread across the state, Rudy can’t watch every worker. That’s why she relies on her supervisors and conducts regular audits.
While auditing each mill, she can also access the standard operating procedures for each site by logging into her EHS management system from her mobile phone. She can check the JHA for a particular job, see what the recommended procedures are and how that compares to how the worker is doing the job.
Using a comprehensive EHS management system has helped Rudy manage the risks most common to her industry. It has also allowed her to track incidents and near-misses and take proactive steps to avoid them.