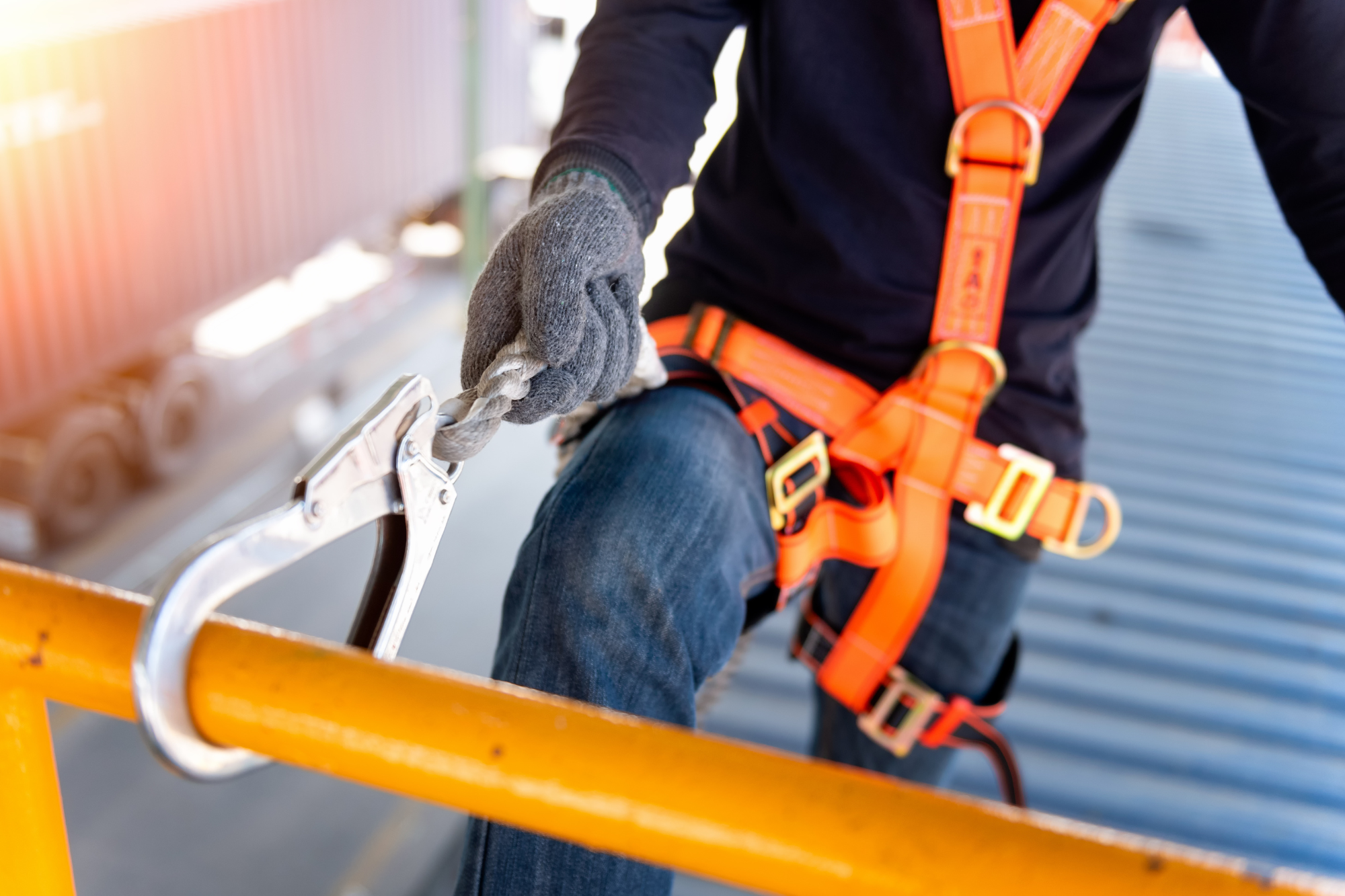
Leverage OSHA’s top 10 violations to reduce safety risks
Each year, the Occupational Safety and Health Administration (OSHA) releases its list of the most frequently cited violations for its fiscal year. This list highlights the key areas where workplaces commonly fall short of safety standards, providing valuable insights into the hazards that pose the greatest risks to employee health and safety. Understanding these top violations not only helps employers prioritize their compliance efforts but also plays a critical role in preventing accidents, reducing injuries, and fostering safer work environments across industries.
Below are the top 10 most frequently cited violations FY224 (Oct. 1, 2023-Sept. 30, 2024).
1. Fall Protection – general requirements (29 CFR 1926.501)
Free resource: Using job hazard analysis to mitigate fall hazards
2. Hazard Communication – general industry (29 CFR 1910.1200)
Free resource: Guide to identifying and classifying chemical hazards
3. Control of Hazardous Energy (lockout/tagout) – general industry (29 CFR 1910.147)
Free resource: Complete guide to creating an effective lockout/tagout program
4. Ladders – construction (29 CFR 1926.1053)
Free resource: Ladders training requirements for the construction industry
5. Respiratory Protection – general industry (29 CFR 1910.134)
Free resource: PPE for manufacturing: Protecting employees from head to toe
6. Powered Industrial Trucks – general industry (29 CFR 1910.178)
Free resource: 5 forklift safety guidelines every employer should follow
7. Fall Protection Training – construction (29 CFR 1926.503)
Free resource: How to lead an effective toolbox talk to prevent fall hazards
8. Scaffolding – construction (29 CFR 1926.451)
Free resource: Walking-working surface safety: Tips to prevent slips and falls
9. Eye and Face Protection – construction (29 CFR 1926.102)
Free resource: PPE audit guide for employers – how effective is your program?
10. Machine Guarding – general industry (29 CFR 1910.212)
Free resource: Q&A: Are emergency stops required on machinery? If so, where are they required?
Employers who know and understand OSHA’s most cited violations can use the list as a tool to:
- Implement proactive safety measures: By knowing which violations are most common, employers can proactively focus their efforts on those areas. Emphasis in these areas can help prevent injuries and illnesses, which can be costly in terms of worker compensation claims, lost productivity, and potential fines.
- Identify training gaps: Employers can improve and create even more targeted training. For example, if fall protection is a common violation, employers can emphasize those areas and the use of proper fall protection equipment and following safety procedures when working at heights.
- Prepare themselves for an inspection: Employers who familiarize themselves with the top violations can better prepare themselves for an agency inspection. Addressing potential hazards ahead of time enables employers to reduce the likelihood of citations and fines.
- Improve workplace safety culture: Focusing on the high-risk areas listed demonstrates a commitment to safety from the top down, leading to a more vigilant workforce and a safer overall work environment.
OSHA’s top-10 list serves as a clear reflection of the agency’s enforcement priorities, offering a way to quantify OSHA violations, track trends year over year, and identify critical areas for employers to address. While this list provides valuable data on the most common compliance gaps, it represents only a fraction of the challenges organizations face in maintaining a safe workplace. True safety leadership requires looking beyond regulatory checkboxes to understand the underlying risks and behaviors that contribute to hazards.
Employers committed to superior safety performance recognize that compliance is the baseline, not the destination. The goal is to protect workers from harm through proactive risk management, continuous improvement, and a culture that prioritizes safety at every level. This approach demands ongoing attention, informed decision-making, and an organizational mindset that values prevention over punishment. By focusing on sustainable safety practices rather than solely avoiding citations, employers can create environments where employees are engaged and empowered to contribute to workplace safety.