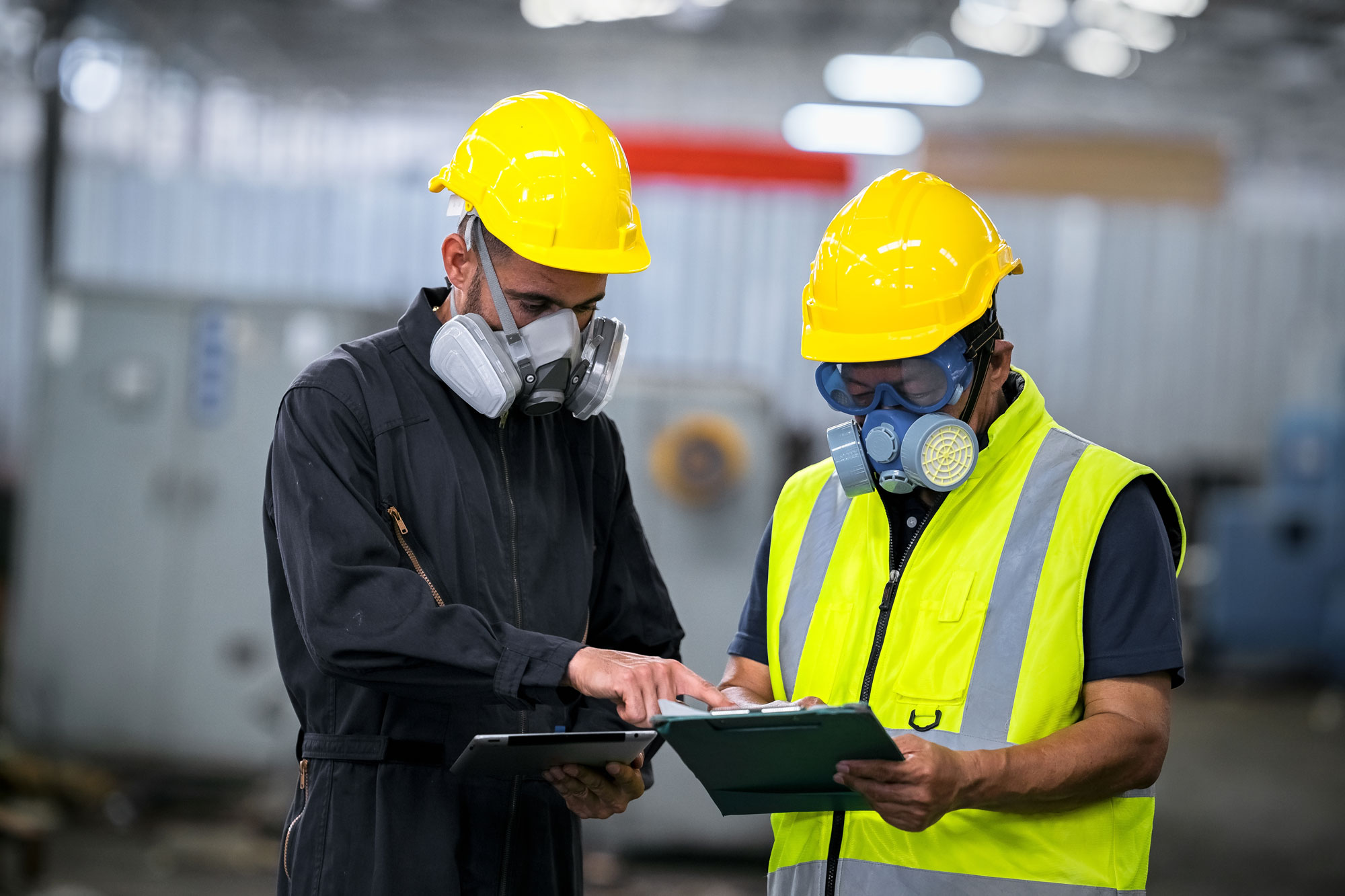
Keeping the workplace safe from chemical hazards
Hazardous chemicals are found in many work environments, from manufacturing to farming, and employees often work with or near these substances.
The physical and health hazards associated with hazardous substances used in the workplace pose significant risks to the health and safety of employees and to nearby equipment and property. Therefore, if hazardous chemicals are present in the workplace, it’s essential—and mandated by federal regulation— for employers to establish a program that educates employees about these hazards. Employees must also actively use the information provided.
Know the regulations
The Occupational Safety and Health Administration’s (OSHA) Hazard Communication Standard (HazCom), under 29 Code of Federal Regulations (CFR) 1910.1200, requires that employers ensure employees have access to information about the chemicals in their workplace, the potential hazards those specific chemicals present , and how to protect themselves and their coworkers. To accomplish this, HazCom:
- Requires that the hazards of each chemical substance be identified and classified. The manufacturer or importer typically provides this information with the chemical as it is distributed and sold.
- Specifies what information goes into a safety data sheet (SDS) and the access employees must have to this information.
- Specifies how chemical containers must be labeled.
- Requires employees to receive information and training on the hazardous chemicals with which they work.
- Requires employers to develop and implement a written hazard communication program for their facility that details how the facility will implement the various components of HazCom.
Know the chemicals
Before working with any hazardous chemical, employees need to take the time to learn about the chemical. The SDS provides the most complete information about chemicals. Every SDS has an identical 16-section format that provides a detailed written description of the chemical, including:
- Identification of the hazards;
- Precautions to take to avoid exposure;
- First-aid information, including symptoms of exposure and treatment;
- Suitable firefighting techniques and equipment, as well as additional chemical hazards that may exist because of the fire;
- Emergency procedures, equipment, and appropriate measures to contain and clean up a spill;
- Precautions for handling and storing the chemical, including chemical incompatibilities;
- Exposure limits, recommended engineering controls, and recommended personal protective equipment (PPE); and
- Guidance on proper disposal practices and safe handling of waste chemicals.
SDSs must be immediately available to employees in their workspace so they can access this information at any time.
In addition, all containers of hazardous chemicals must be labeled, and employees should familiarize themselves with the chemical label information. The contents of a chemical label on a container entering or leaving the facility are prescribed by the HazCom requirements under 29 CFR 1910.1200(f) .
Containers used in the facility must be labeled with a combination of a product identifier, along with words, pictures, and symbols clearly communicating general information about the chemical’s hazards. Written materials containing the information in 29 CFR 1910.1200(f) must be immediately available.
Embrace safety training
HazCom requires that employees who may be exposed to hazardous chemicals in their work area receive training at the time of their initial assignment and whenever a new chemical hazard is introduced that they have not been trained on.
The training must cover:
- HazCom requirements under 29 CFR 1910.1200;
- The operations in the work area that use hazardous chemicals;
- The location, availability, and details of the written HazCom program for the facility, including information about the labeling system and access to SDSs;
- The methods used to detect the presence or release of a hazardous chemical;
- The hazards of the chemicals in the work area; and
- The measures that can be taken to protect oneself from such hazards, including appropriate PPE.
Hazardous chemicals are dangerous and potentially fatal if not used and handled properly. The information provided during HazCom training may save your life or the life of a coworker.
Build a positive safety culture
Employers bear much of the responsibility for informing employees about the dangers of hazardous chemicals used in their jobs. However, for hazard communication to be effective, employees must actively engage with the information provided to them. This is why training is essential. Fostering a strong safety culture within your organization is vital for encouraging employees to prioritize safety in the workplace.
Prioritizing safety at every level of your business and taking clear actions to show that safety matters will encourage employees to embrace a safety culture and take it seriously. A strong safety culture will motivate workers to engage with the training and learn about the hazardous chemicals in the workplace, leading to a safer environment. Effective communication about chemical exposure is key to ensuring that all employees understand the risks and can take appropriate precautions.