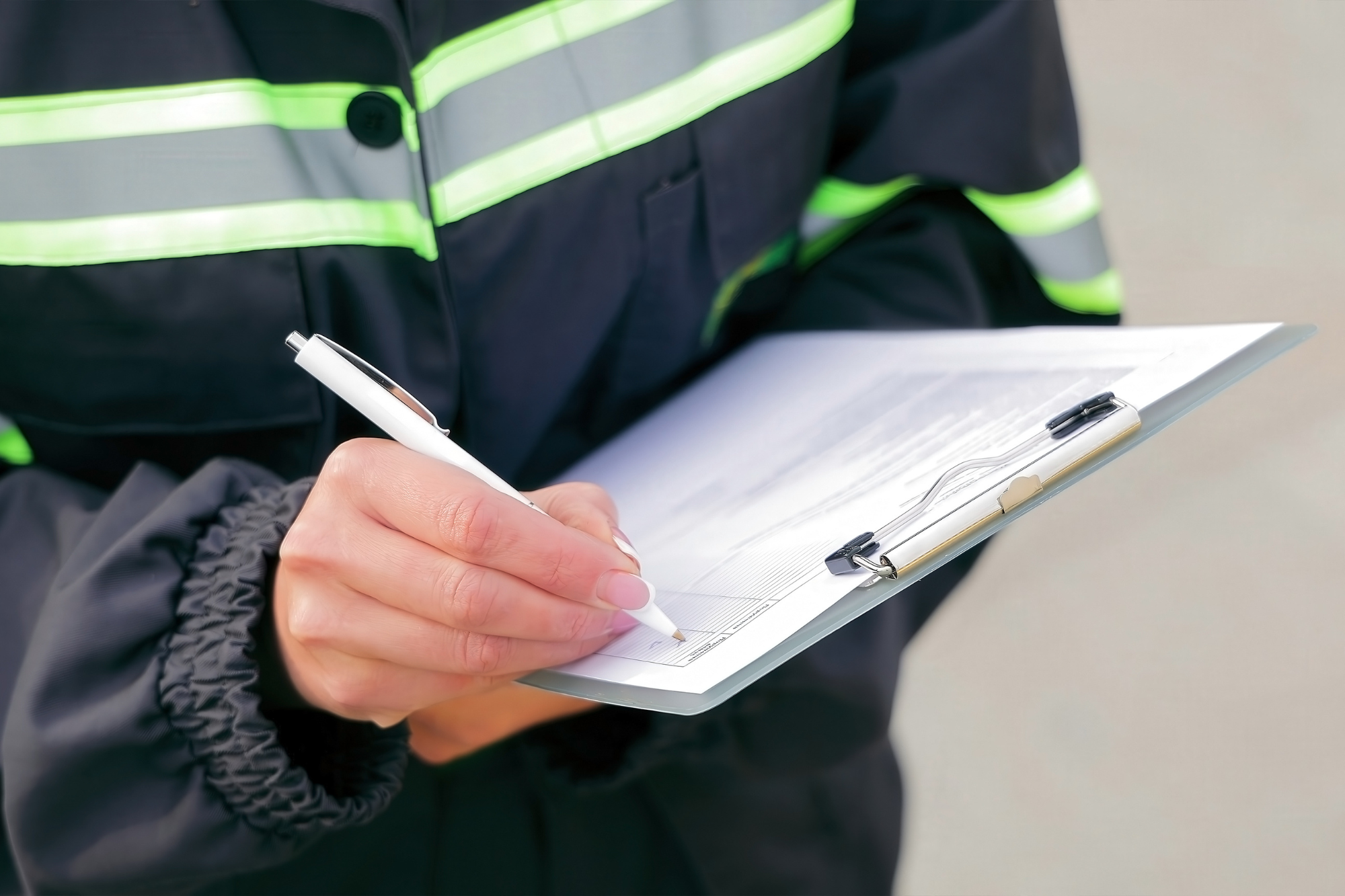
How to effectively track your company’s safety performance
Tracking safety performance is a critical part of protecting your team and strengthening your operations. When you don’t have a clear view of how your safety programs are performing, it can be more difficult to make informed decisions or respond to risks before they escalate.
Gaps in tracking can also lead to missed opportunities for improvement, increased exposure, and costly incidents. Staying ahead requires consistent evaluation and a clear understanding of what the numbers are telling you.
This article will walk you through straightforward ways to measure your company’s safety performance and use that insight to take meaningful action. With the right approach, you can stay ahead of potential issues, build trust across your organization, and lead with confidence.
Lagging indicators
What they are and why they’re important
Lagging indicators measure outcomes that have already occurred. While they don’t help prevent incidents on their own, lagging indicators are essential for understanding where your safety program has fallen short and where improvements are needed.
These indicators provide statistics on workers’ past compliance with safety guidelines. They include
- Lost workdays
- Workers’ compensation payouts
- Occupational Safety and Health Administration (OSHA) recordable injuries
- Injury frequency and severity
They show where injuries are happening, how often incidents occur, and how serious the consequences are. This data helps you evaluate the effectiveness of your existing programs and meet reporting requirements, all while demonstrating accountability to leadership. Additionally, tracking these figures over time helps identify patterns and supports more informed decisions about where to focus your efforts.
How to measure lagging indicators
To measure lagging indicators, begin by gathering accurate data from your existing records. Use sources like incident reports, OSHA logs, and workers’ compensation claims. Common formulas include the Days Away, Restricted, or Transferred (DART) rate, and the Total Case Rate (TCR).
Once you’ve established a consistent measurement process, use it to guide targeted improvements. Whether you’re refining training programs, adjusting workflows, or addressing repeat hazards, reliable lagging indicator data helps you move forward with purpose and clarity.
Leading indicators
What they are and why they’re important
To get a full picture of your safety performance, you need more than just incident data. Leading indicators measure the proactive steps your organization takes to prevent injuries and improve conditions before problems occur. These include activities like safety training, equipment inspections, near-miss reporting, employee feedback, and regular audits.
Leading indicators are important because they focus on what can be controlled. They shift the mindset from reacting to incidents to actively reducing risks. These metrics help you evaluate engagement, spot early warning signs, and create a stronger safety culture. They also show your team that safety is a shared responsibility—something built into everyday work, not just tracked after an event.
How to measure leading indicators
Start by identifying the preventive activities most relevant to your operations. Track things like
- Training participation rates
- Completion of safety checklists
- The number of reported near misses
Choose metrics that are easy to measure, clearly understood by your team, and aligned with your safety goals.
Over time, you can evaluate whether improvements in leading indicators are linked to reductions in injuries or other incidents. For example, more consistent equipment inspections may lead to fewer mechanical failures. When tracked and communicated effectively, these metrics support continuous improvement and build accountability at every level.
Repeat offenders and trends
Lagging and leading indicators provide valuable insight into both risk and progress, but the real value comes from identifying patterns across your organization. Track trends over time to uncover repeat issues, high-risk areas, and the people or processes most associated with incidents or near misses. Pay close attention to work groups and individuals who appear frequently in incident reports. Determine whether the same hazards are recurring and whether they are limited to one location or present across multiple sites.
Equally important is recognizing where progress is happening. Identify the teams and individuals contributing to improvements in leading indicators, such as increased training participation or proactive hazard reporting. Understanding what drives those improvements can help you replicate their success across the organization.
This well-rounded view of both setbacks and progress gives you the insight needed to act with clarity and purpose. You’ll be better equipped to correct problem areas, reinforce what’s working, and lead your safety program forward with confidence.
Digital incident tracking
Use a digital incident tracking system to simplify tracking indicators and trends. Customized, user-friendly forms allow for accurate recording of incidents, and filters can be applied to analyze data based on employees, teams, divisions, and worksites. Access to organized historical data enables quicker data analysis and more efficient action-taking.
Digital tools also reduce the risk of errors and missed details that can happen with paper-based systems or scattered spreadsheets. With everything stored in one centralized location, safety teams can easily spot recurring issues, respond faster, and stay prepared for audits. Investing in the right system helps you lead with clarity, improve response times, and stay focused on what matters: keeping your team safe.
Centralize your safety efforts with confidence
Managing safety performance takes more than tracking isolated data points. With information coming from training programs, job safety analyses, audits, reports, and investigations, it quickly becomes too complex to handle manually. You need a system built to keep up.
Turn data into action with EHS Hero®
From near-misses and training completion rates to incident trends and root causes, BLR’s EHS Hero helps you track both leading and lagging indicators—with centralized tools and real-time visibility, you can monitor performance, identify gaps, and make faster, more informed decisions all in one platform. Get the visibility you need to prevent incidents, improve safety culture, and stay audit-ready.