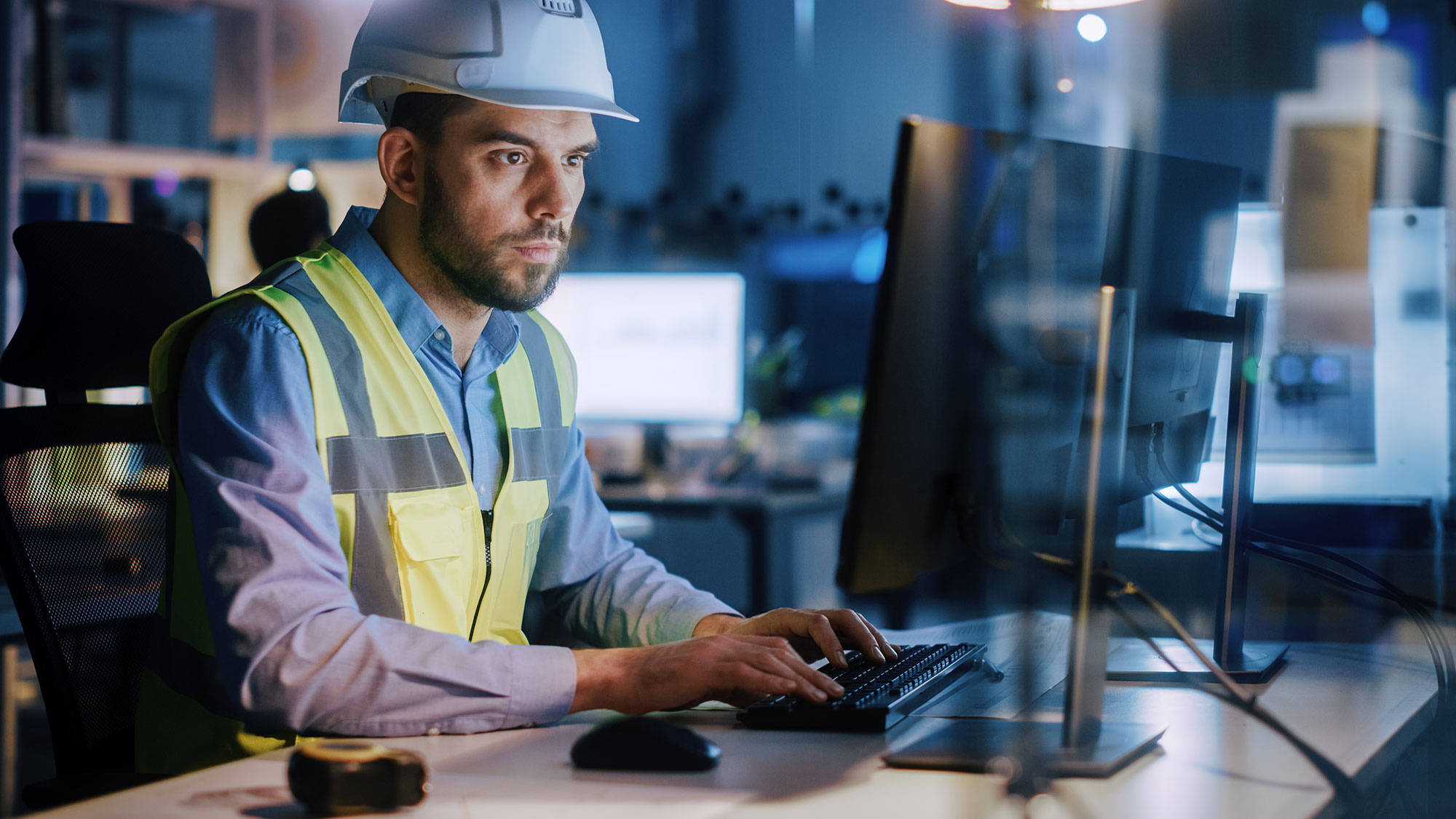
How to build a safety program in 8 steps
Implementing a safety program is integral for preventing injuries and illnesses in the workplace, increasing productivity, and engaging employees with safety. Whether you’re a small business or a large enterprise, here are 8 steps you can use to build an effective safety program.
Step 1: Make a commitment to safety
It is important to make safety a company-wide commitment. Include safety in your company mission statement and involve the executives in setting safety related goals. Document these goals so that you can track progress and identify areas for improvement. This step will help foster a culture of safety and keep safety top of mind for the entire organization.
Step 2: Understand the requirements in place for your industry
To learn the requirements for your industry, check out the resources made available by OSHA and speak with other professionals in your industry. Sometimes it pays to bring in an outside consultant for your industry even if it is just a safety manager from another similar company. You should document these requirements and advice so you can ensure they all are implemented.
Step 3: Identify workplace hazards and assess risks
Hazard identification is the cornerstone of prevention. Engage employees at all levels—those closest to the work often provide the clearest insights.
Evaluate
- Physical hazards such as machine guarding or floor conditions
- Environmental exposures like heat, noise, or airborne contaminants
- Task-specific risks including confined spaces or energized equipment
- Cultural factors like safety perceptions and behavior patterns
Use a risk assessment framework to prioritize corrective actions and track progress over time.
Step 4: Develop processes and programs
These processes and programs should be specifically tailored to meet the requirements from Step 2 and address the issues from Step 3. They should also hold both management and employees accountable for safety. It is best to have them written and made accessible to all employees.
The regulations that require a formal written program are as follows:
- Hazard communication program
- Lockout/tagout program
- Respiratory protection program
- Personal protective equipment (PPE)
- Bloodborne pathogens post-exposure plan
- Emergency action plan
- Permit-required confined spaces
- Electrical safety
- Fire prevention plan
- Hearing conservation program
- Trenching and excavation safety
Step 5: Educate and empower your workforce
Educating your employees on policies and procedures any other relevant information is key to keeping them safe.
As a best practice, deliver training:
- During new hire onboarding
- When employees change roles or tasks
- Whenever new equipment, processes, or chemicals are introduced
- When new hazards are identified
- On a regular basis for refresher and required compliance training
Use a mix of delivery methods (in-person, online, hands-on) and keep training records up to date.
Step 6: Investigate and track all incidents and near-misses
Every incident—no matter how minor—is an opportunity to learn and improve. Conduct thorough investigations that go beyond blame to uncover root causes. From there, implement corrective and preventive actions, and update related procedures or training. Capturing lessons learned helps prevent recurrence and strengthens organizational learning.
Step 7: Regularly review and improve your program
An effective safety program is dynamic, not static. Conduct annual reviews (or more frequently as needed) of your safety documentation, training effectiveness, and program performance. Internal audits, gap analyses, and worker feedback are all valuable tools for continuous improvement.
Step 8: Leverage EHS management technology
Digital tools can streamline compliance, centralize documentation, and improve visibility into safety performance.
The ideal EHS management system should support:
- Procedure and policy development
- Training creation and tracking
- Audit execution and follow-up
- Real-time incident reporting and investigation
- KPI monitoring and dashboarding
Explore proven strategies and tools to strengthen your program
Building a safety program isn’t a one-time project—it’s an ongoing commitment to your workforce and your mission. With the right structure, leadership support, and tools in place, your safety efforts can drive lasting cultural and operational impact.