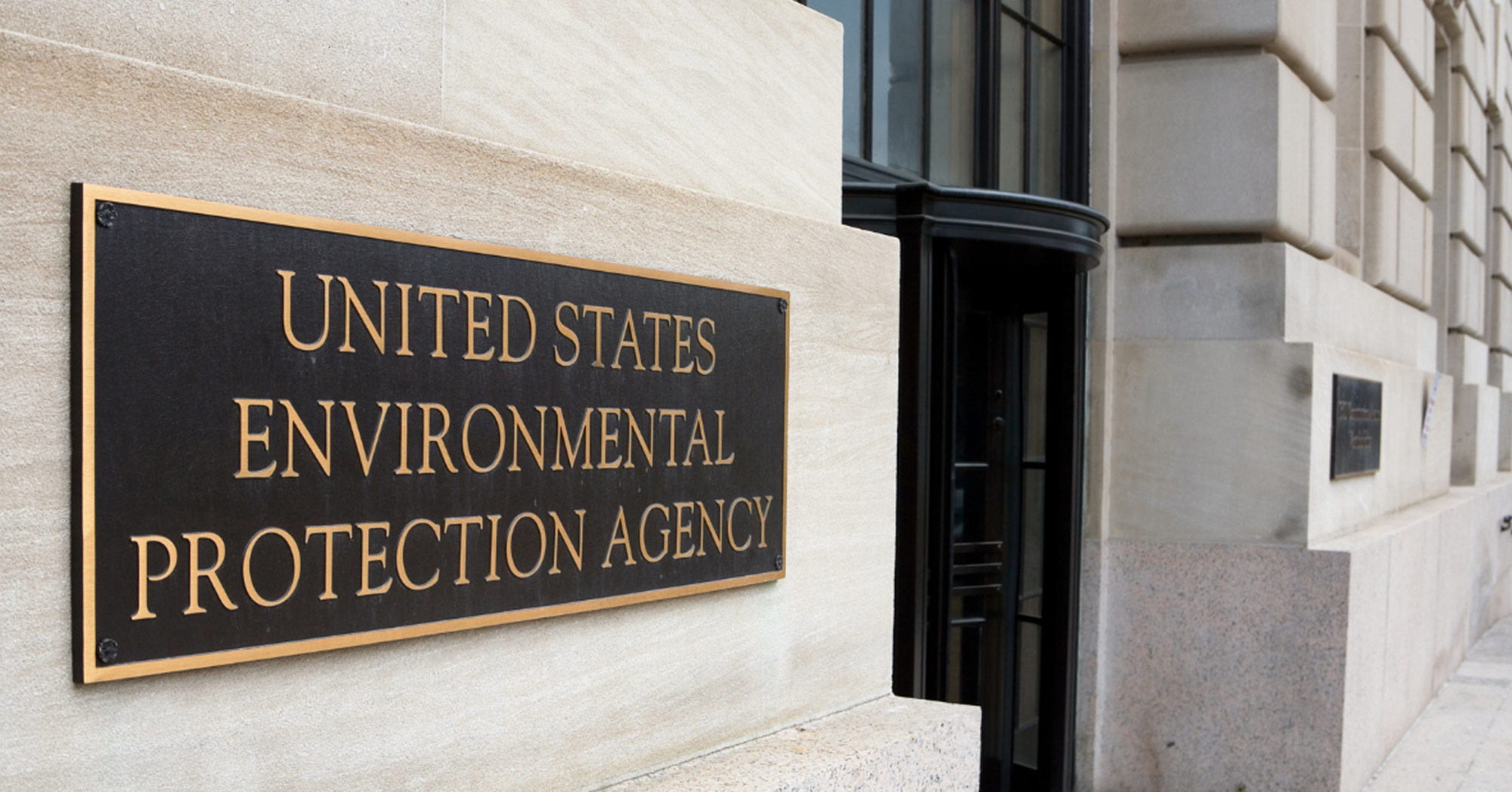
EPA training requirements
The Environmental Protection Agency (EPA) administers the rules and regulations that protect, preserve, and clean up the air, waterways, and land of the United States. If you generate, transport, treat, store, or dispose of hazardous waste, you will also need to comply with federal EPA training requirements and regulations.
EPA training requirements focus on workplace activities designed to eliminate the release of pollutants and wastes into the environment, both on-site and off-site. These include asbestos, lead abatement, and certain other highly toxic or cancer-causing materials. Training requirements related to environmental protection vary by industry and job responsibilities.
Here are some broad overviews of some of the EPA training requirements:
- Asbestos: Individuals who handle, remove, or disturb asbestos-containing materials must receive specific training in accordance with EPA regulations. Asbestos training includes courses on how to identify asbestos-containing materials, how to protect oneself and others from exposure, and how to properly handle and dispose of asbestos materials.
- Lead: Individuals who perform lead-based paint activities must be trained and certified on the proper handling and disposal of lead-based paint, as well as techniques for minimizing the risk of exposure. These individuals include renovators, painters, and other professionals who work in buildings that contain lead-based paint.
- Hazardous waste: Anyone who handles hazardous waste must be trained on how to properly identify, handle, store, and dispose of hazardous waste, as well as how to respond in the event of a spill or an emergency, in accordance with EPA regulations.
- Spill Prevention, Control, and Countermeasure (SPCC): The EPA requires certain facilities, such as oil storage facilities, to develop and implement SPCC plans to prevent oil spills. Individuals who work at these facilities are required to receive training on how to implement the SPCC Plan, as well as how to respond in the event of a spill.
- Stormwater management: The EPA requires certain industries, such as construction and industrial facilities, to implement stormwater management plans to prevent pollution of waterways. Individuals who work in these industries are required to receive training on how to implement stormwater management plans and prevent stormwater pollution.
These are just a few examples of EPA training requirements. The specific training requirements depend on the industry and the type of work being performed. It’s important for individuals and companies to research and comply with all applicable EPA training requirements to ensure the safety of workers and the environment.
Tips for training compliance
Employers can comply with EPA training requirements by informing, educating, and training their employees to protect themselves, the public, and the environment from workplace hazards. The EPA and its regulatory partners conduct compliance inspections to determine whether facilities are in compliance with statutory and regulatory program authorities.
Here are 10 tips to help create a training program that meets federal EPA requirements.
1. Identify relevant regulations.
Research the EPA regulations applicable to your industry and operations. Determine which training requirements apply to your employees, such as HAZWOPER, Emergency Planning and Community Right-to-Know Act (EPCRA), or Resource Conservation and Recovery Act (RCRA) training.
2. Assess employee roles.
Identify which employees need specific training based on their job duties and responsibilities. Determine their current knowledge and skill levels, and identify areas where additional training is needed.
3. Develop a training plan.
Create a comprehensive training plan that covers all required topics and includes goals, objectives, and timelines. The plan should include initial training for new employees, as well as refresher training for existing employees.
4. Use appropriate training materials.
Develop or source high-quality training materials that are tailored to your industry and operations. Ensure the materials cover all required topics and are engaging and easy to understand.
5. Choose qualified trainers.
Select trainers who are knowledgeable about the EPA regulations and have experience in delivering effective training. They should be able to adapt their teaching style to meet the needs of different learners.
6. Implement hands-on and interactive training.
Incorporate hands-on activities and interactive elements, such as case studies, group discussions, and simulations, to help employees better understand the material and apply it to their job duties.
7. Monitor and evaluate progress.
Track employee progress throughout the training program and evaluate their understanding and retention of the material. Adjust the training as needed based on feedback and performance.
8. Provide ongoing support.
Offer ongoing support to employees after the training, such as access to resources, guidance, and opportunities for additional training and development.
9. Maintain records.
Keep detailed records of all training activities, including attendance, completion dates, and test results. This documentation will be essential for demonstrating compliance during inspections or audits.
10. Review and update the training program.
Periodically review and update your EPA training program to ensure it remains current and relevant. Stay informed about changes in regulations and industry best practices and incorporate new information into your training materials and methods.
Employers should familiarize themselves with the training requirements that apply to their employees and business, design and implement effective programs using qualified trainers, and thoroughly document all training activities and retain records of employee attendance at all completed trainings.