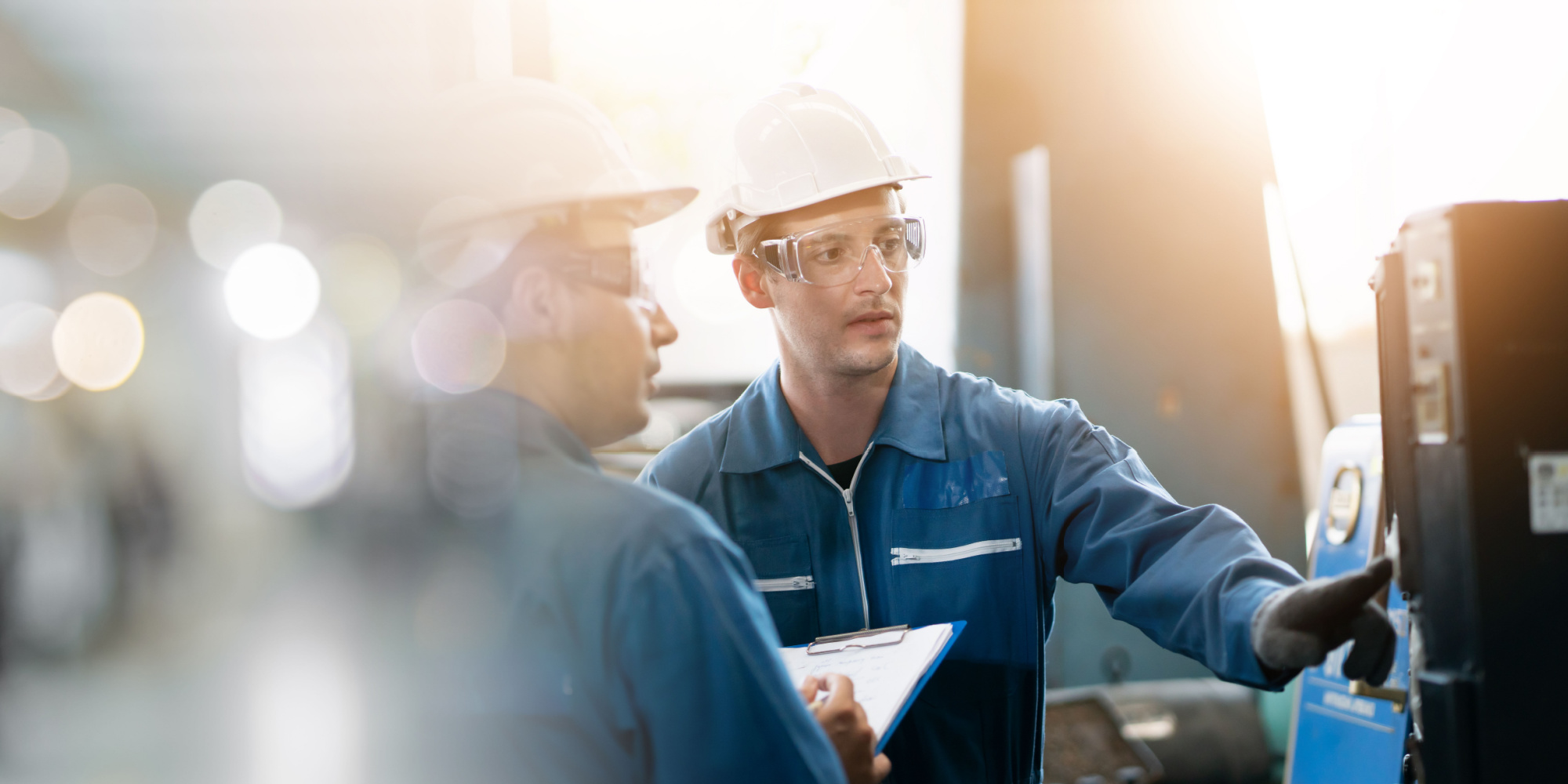
Enhancing worker safety when operating heavy machinery
Working around heavy machinery presents significant challenges and risks. It’s unrealistic to completely eliminate all hazards in an industrial setting where complex tasks are carried out using large pieces of equipment. However, as a responsible business leader, there are proactive measures you can take to minimize the likelihood of accidents and promote a safer work environment. Employee injuries not only hamper productivity but also have a negative impact on company profitability and employee morale.
Your employees rely on you to establish a safe workplace where their well-being is prioritized. Understanding the necessary steps to create such an environment can be overwhelming for employers. To assist you in this endeavor, we offer a few valuable tips to optimize workplace safety.
Don’t use defective equipment
It’s the employer’s responsibility to ensure all machinery is maintained in good working condition. Neglecting this duty and failing to prove negligence can also result in significant financial repercussions, often leading to legal fees attributed to lawsuits filed by injured employees.
To keep your workers safe and avoid legal entanglements, it’s crucial to regularly update your equipment according to the manufacturer’s recommendations. Additionally, staying updated on the latest technological advancements within your industry is essential. As safety improvements are continually made, implementing the newest safeguards can effectively save lives and prevent workplace injuries.
Lockout/tagout
Lockout/tagout (LOTO) is a widely recognized procedure in industrial work settings that prioritizes accident prevention by ensuring effective communication regarding machinery usage. A crucial component of this procedure is the use of proper LOTO labels, which provide essential information for workers who may encounter the machine.
Continual training
Human error often plays a significant role in workplace accidents involving heavy machinery, regardless of the level of training provided. Over time, when attendance becomes optional or when enough time has passed, adherence to safety protocols tends to decline. This leads to an increase in unnecessary risks, the neglecting or complete disregard of safety precautions, and the failure to follow procedures intended to ensure safety.
To address these issues, implementing ongoing education programs that prioritize safety is crucial. Additionally, testing your employees to ensure their understanding of industry-specific safety protocols and the importance of adhering to them can be beneficial.
While working around heavy machinery is sometimes unavoidable, it’s possible to make it safer. By implementing these changes at your company, you are likely to witness improved performance and safety outcomes.