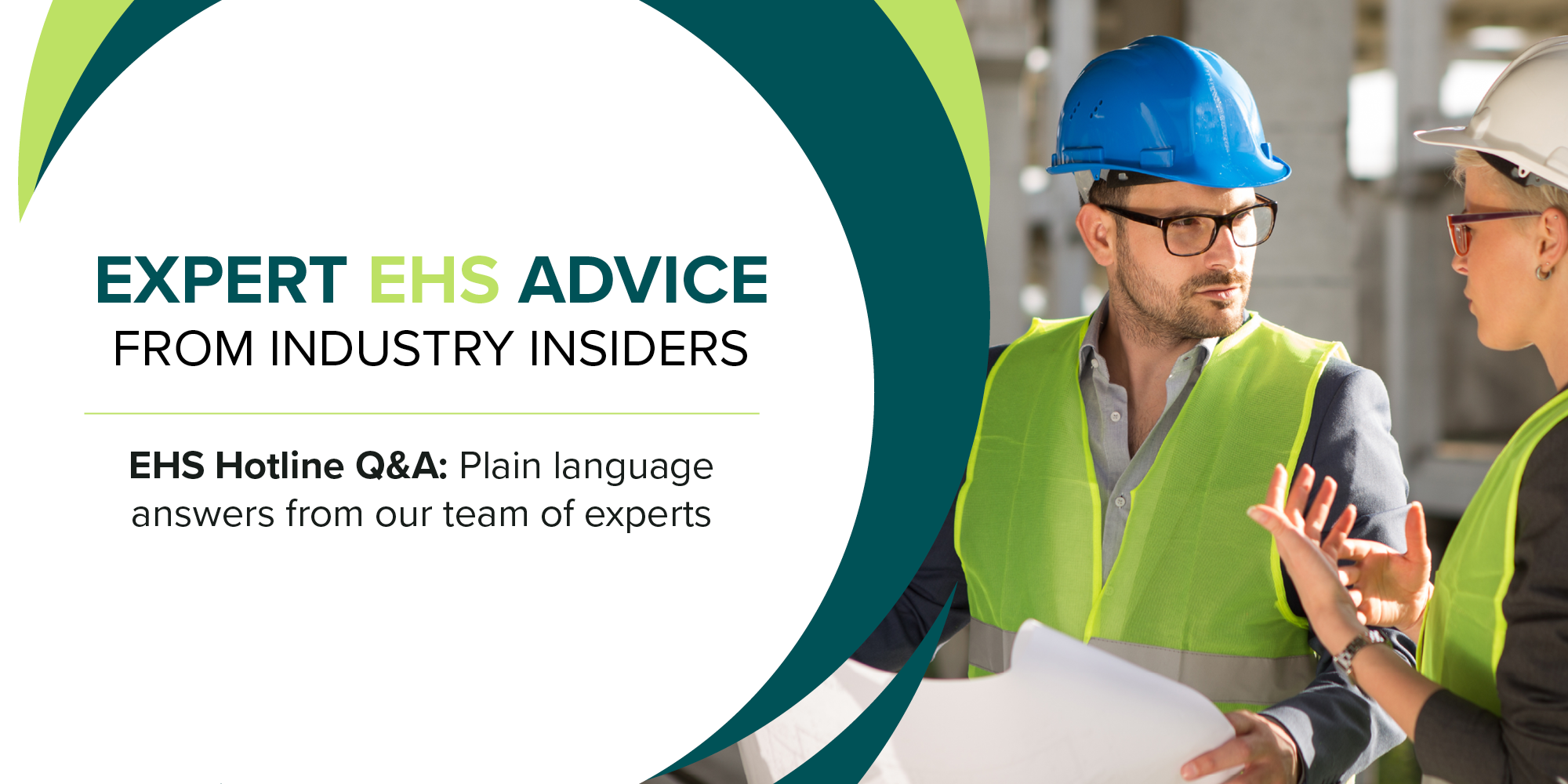
Q&A: Is lockout required for equipment not serviced by employees?
Does a business need to have energy control procedures to lockout equipment if no workplace employee performs service and repair on the equipment the employer utilizes?
A business needs energy control procedures to lockout equipment when an authorized employee implements any part of a lockout/tagout procedure to permit servicing or maintenance, including energy disconnect and applying a lock. The requirement applies even when no workplace employee performs the service and repair on the equipment, because that employee is implementing a part of the procedure that permits the servicing and maintenance work by a contractor or someone else.
A worker is considered an authorized employee if they lock out or tag out machinery or equipment to perform servicing or maintenance or implements a lockout and/or tagout system procedural element on machinery or equipment to permit servicing or maintenance.
Authorized employees implement a lockout or tagout procedural element if they:
- Perform energy source isolation;
- Implement lockout and/or tagout on machinery or equipment;
- Dissipate potential (stored) energy;
- Verify energy isolation;
- Implement actions to remove locks or tags; or
- Test or position machinery or equipment.
According to the lockout/tagout regulation at 29 Code of Federal Regulations (CFR) 1910.147(a)(1) and 1910.147(f)(2), if an outside contractor services or maintains machinery (e.g., an elevator), the onsite employer and the contractor must inform each other of their respective lockout or tagout procedures.
The onsite employer also must ensure that his or her employees understand and comply with the restrictions and prohibitions of the contractor’s energy control program.
What is EHS Hotline?
Subscribers of EHS Hero get access to our team of in-house subject matter experts. EHS Hotline allows subscribers to submit questions and receive timely, thorough, and plain-language answers from our team of experts—complete with resources and references.
The purpose of EHS Hotline is to help connect workplace employment, safety, and environment questions to the material provided by BLR on its subscriber websites. While the service is defined as providing advice, it is assistance to help bridge the gap between the BLR compliance resources and our client’s workplace issues. It is not a legal opinion or replacement for seeking legal counsel.