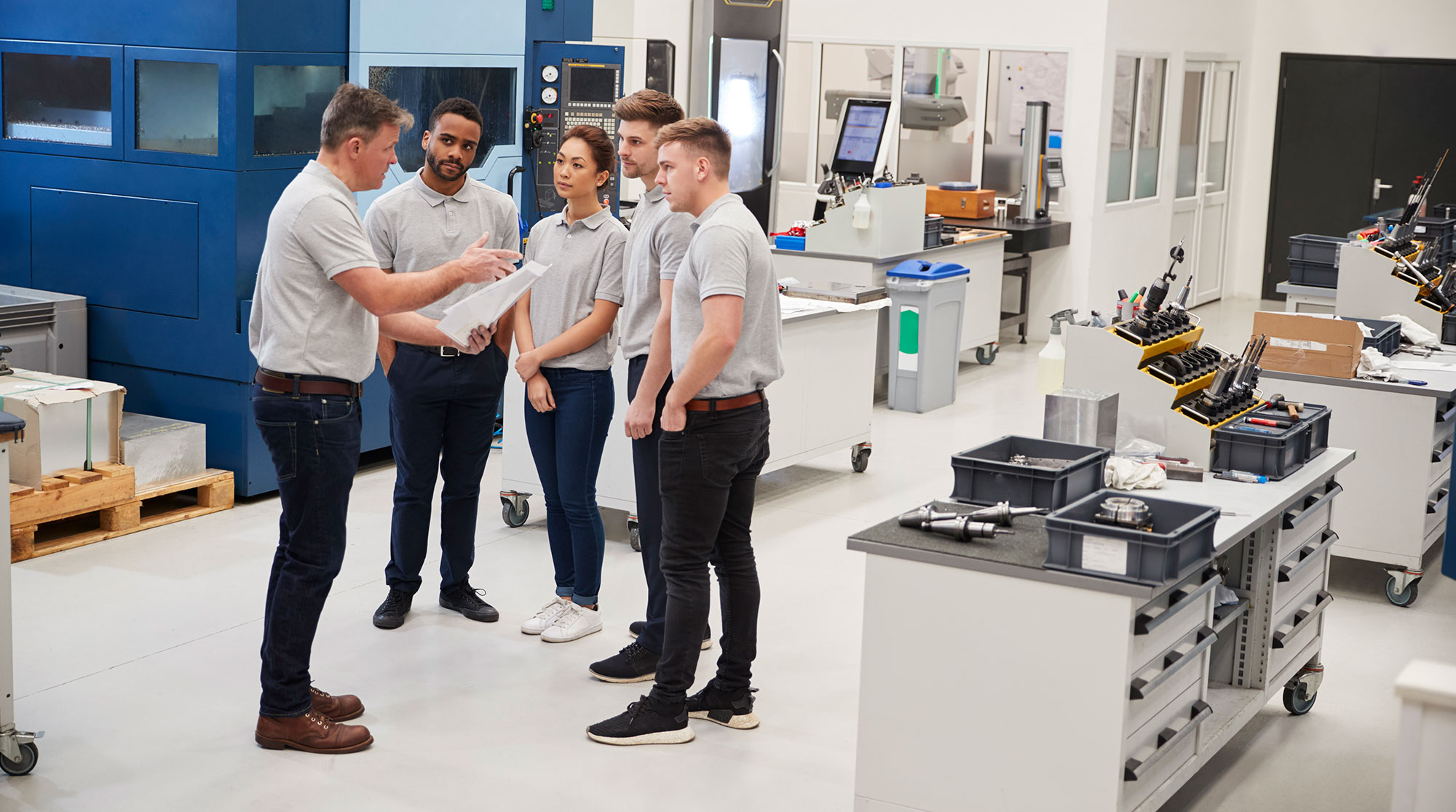
Bloodborne pathogens exposure control and training
Bloodborne pathogens are small organisms found in blood or other infectious materials. The most common bloodborne pathogens can lead to diseases such as hepatitis B, hepatitis C, and HIV/AIDS.
For a bloodborne pathogen to spread, the bodily fluids of an infected person must enter into the bloodstream of another person. Infections spread at work when someone with an infection gets their blood into someone else’s body through a cut. This is the main way infections spread in the workplace.
The transmission of infections occurs through blood contact.
What the bloodborne pathogens standard says employers must do
The OSHA Bloodborne Pathogens standard (29 CFR 1910.1030) requires employers to eliminate, or at least minimize, the hazards of occupational exposure to bloodborne pathogens. Employers must create a written bloodborne pathogen exposure control plan to protect workers at risk of exposure to blood or other potentially infectious materials. They must also implement a combination of safety measures including engineering and work practice controls, personal protective equipment (PPE), employee training, and offering potentially exposed workers the vaccination against hepatitis B.
There are various jobs that are at risk of exposure to blood and other infectious materials. The bloodborne pathogens rule covers these jobs. This includes trained employees who give first aid, healthcare workers, and even housekeepers and janitors at healthcare facilities.
Bloodborne pathogens training in the workplace
Employers must give bloodborne pathogens training to at-risk workers to help them identify blood and OPIM and to protect themselves against exposure. Training must include universal precautions. “Universal precautions” require treating all human blood and OPIM as if they contain pathogens.
Common universal precautions
- Thoroughly wash hands after any potential exposure.
- Offer the Hepatitis B vaccination to all employees who have a reasonable chance of occupational exposure. OSHA requires this in the United States.
- Utilize engineering controls if feasible, such as using sharps containers with self-sheathing needles or blunt-tipped needles.
- Provide and require employees to wear appropriate PPE like gowns, eye protection (goggles or face shields), masks, and other protective gear as needed by the specific job tasks.
- Regularly clean potentially contaminated surfaces with a disinfectant, such as a bleach solution.
- Use labels and signs to warn workers of potential hazards and proper procedures.
- Establish post-exposure procedures for response to an exposure incident, including medical evaluation and follow-up.