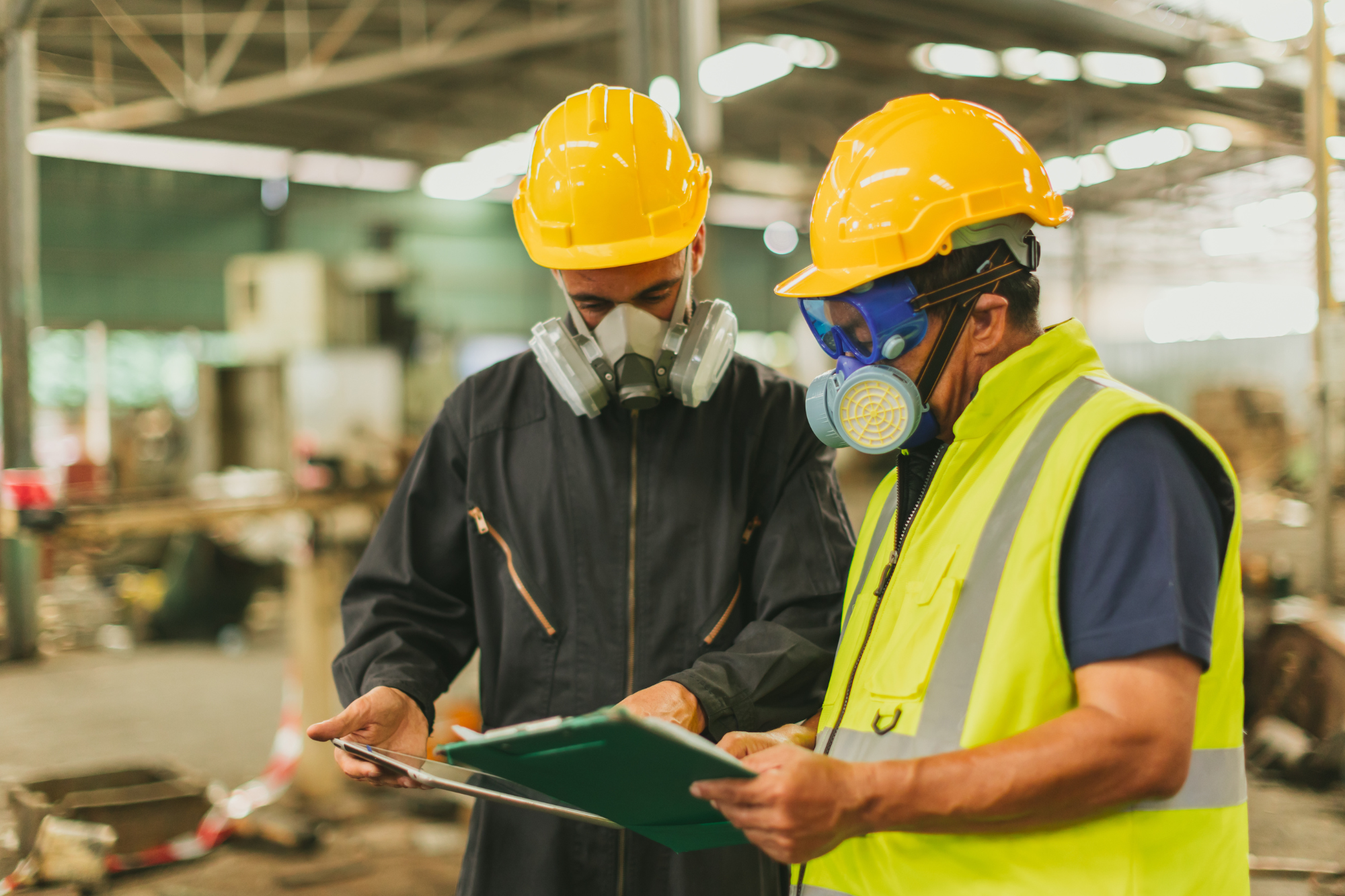
Best practices for effective incident investigations
The U.S. Bureau of Labor Statistics reports that more than a dozen workers die every day in American workplaces, millions suffer serious workplace injuries each year, and tens of thousands are sickened or die from diseases resulting from their chronic exposures to toxic substances or stressful workplace conditions.
These events cause much suffering and great monetary loss to workers and their families, and result in significant costs to employers and to society. Many more “near misses” or “close calls” also happen; these are incidents that could have caused severe injury or illness but did not, often by sheer luck. All of these harmful incidents and close calls are preventable.
One of the most effective ways for a company to prevent accidents, strengthen its safety culture, and reduce costs related to injuries and illnesses is by implementing a good incident investigation program. By thoroughly investigating incidents, companies can identify root causes and take corrective actions before a serious accident happens.
Incident vs. accident
Before outlining best practices for incident investigations, it’s important to clarify the distinction between an incident and an accident.
The Occupational Safety and Health Administration (OSHA) defines an incident as a work‐related event in which an injury or illness (regardless of severity) and/or fatality or property damage could have occurred, which is why incidents are occasionally called near misses or close calls. OSHA defines an accident as an undesired work-related event in which an injury or illness and/or fatality or property damage did occur. Workplace events, whether they are incidents or accidents, must be investigated to understand what happened and prevent recurrence.
Regulatory overview
The Occupational Safety and Health Administration (OSHA) requires employers to provide a safe workplace for employees.
Under the Occupational Safety and Health Act employers have the responsibility to provide a safe workplace free from serious hazards and comply with all OSHA safety and health standards. They must identify and address safety and health issues proactively. OSHA also mandates that employers prioritize eliminating or reducing hazards by improving working conditions, rather than relying solely on personal protective equipment (PPE) like masks, gloves, or earplugs. Switching to safer chemicals, enclosing processes to trap harmful fumes, or using ventilation systems to clean the air are examples of effective ways to eliminate or reduce risks.
Incident investigation best practices
Investigations are incident‐prevention tools and should be an integral part of an occupational safety and health management program in a workplace. Such a program is a systematic approach to identifying and controlling the hazards in a workplace and should emphasize continual improvement in health and safety performance. When done correctly, an effective incident investigation uncovers the root causes of the incident or ‘close call’ that were the underlying factors. Most importantly, investigations help identify and eliminate hazards, preventing future accidents when corrective actions are taken to address the root causes uncovered during the process.
Prior to an incident in the workplace, employers should establish an incident investigation plan to ensure a timely and effective response when an investigation is needed. As with many processes, preparation and documentation are crucial.
As part of their workplace EHS program, employers should develop a documented process outlining the steps to take in the event of an incident. This written plan should:
- Establish how medical treatment/first aid will be provided for injuries/illnesses.
- Establish a plan to conduct notifications.
- Determine who will participate in the investigation.
- Develop an investigation kit with all the essential tools needed to conduct a thorough investigation (e.g., accident investigation checklist, signs or caution tape, camera, flashlight, tape measurer, gloves, incident report form, witness forms, clipboards, pens, recording device, etc.)
- Determine how you will:
- Conduct interviews with those involved in the incident.
- Record witness statements.
- Secure and document the scene.
- Implement corrective actions.
- Conduct follow-up to ensure corrective actions have been implemented properly.
When a workplace incident occurs, everyone will be busy dealing with the situation at hand. Therefore, it’s important to have a systematic approach for handling and investigating incidents in place beforehand.
If an incident occurs, follow these investigation best practices
- Call or gather the necessary person(s) to conduct the investigation.
- Obtain the investigation kit.
- Secure the area where the incident occurred and preserve the work area as it is.
- Identify and gather witnesses to the event.
- Interview the involved employee(s).
- Interview all witnesses to the event.
- Document the scene with photos, videos, and sketches of the area.
- Take as many notes as possible to help recall the scene.
- Complete the incident report by determining the root cause of the incident and identifying the corrective actions needed to prevent recurrence.
- Implement the appropriate corrective actions to prevent recurrence.
- Follow-up to ensure corrective actions are implemented properly.
- Use the results of the incident investigation to improve current work practices and prevention programs to better control hazards before they result in incidents.
- Communicate the incident details, corrective actions, and key takeaways with employees and supervisors to reinforce lessons learned.
Building a stronger safety culture through effective incident investigations
Remember the purpose of an incident investigation is to learn and prevent, not find fault. Investigating a workplace incident gives employers and employees the opportunity to identify hazards in their operations and shortcomings in their workplace environmental, health, and safety programs. Most importantly, it enables employers and employees to strengthen their commitment to building a strong safety culture.