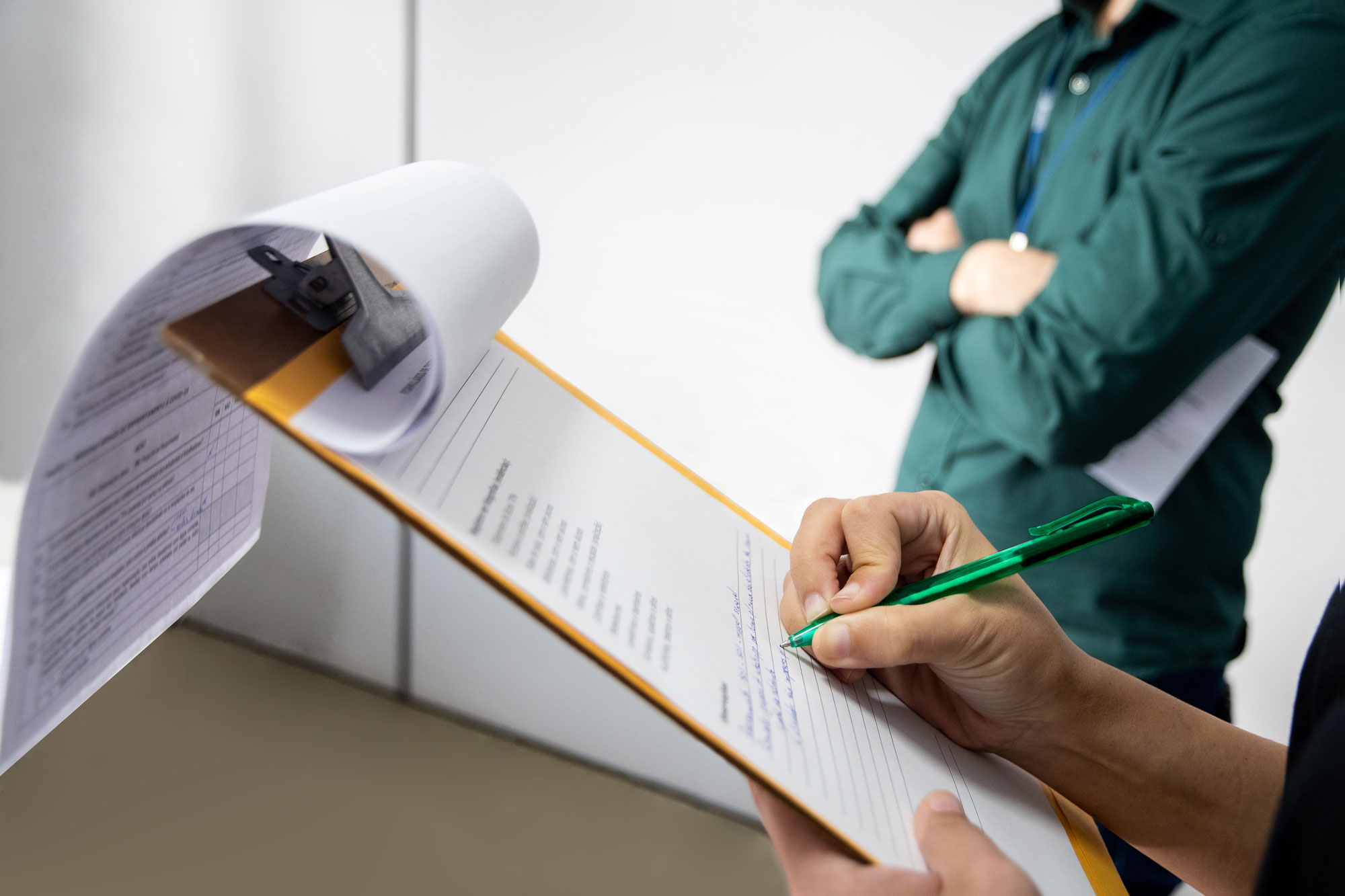
5 Common workplace safety mistakes and how to avoid them
Creating a safe workplace is essential in making employees feel valued, but it’s easier said than done. Many companies still make common safety mistakes that can be found on the Occupational Safety and Health Administration’s (OSHA) list of frequently cited standards.
To ensure greater effectiveness, it’s important for employers to revisit their safety programs and policies. In this article, we’ll discuss some of the most common workplace safety mistakes and provide tips on how to avoid them.
1. Rushing through the training process
In their haste to get employees up to speed, companies often expedite the training process. However, effective training requires sufficient time and planning.
By allocating more time to training, employers can ensure employees are adequately equipped with knowledge about workplace safety, including potential hazards and their appropriate handling. Furthermore, tracking employee progress throughout the training process enables employers to gauge the level of understanding and compliance with safety guidelines.
2. Delaying maintenance and inspections
Machines with issues pose a significant risk for employees operating them and those working in close proximity. To mitigate these risks, regular maintenance and inspections are crucial in identifying potential hazards and implementing prevention measures.
However, companies may be reluctant to shut down machines due to concerns about productivity. To avoid delays in maintenance and inspection, it’s essential to schedule them in advance and adhere to the plan, thereby ensuring the uninterrupted operation of machines and minimizing chances of breakdowns.
3. Neglecting near misses
Workplace safety incidents don’t always lead to injuries, and these non-injury scenarios are often overlooked. However, it’s essential to treat these near misses seriously.
Close calls should be reported, investigated, and tracked, along with any corrective actions they inspire. Taking this proactive approach ensures potential hazards are addressed, preventing future accidents and promoting a safer work environment.
4. Substituting tools for the job
In an attempt to cut costs, companies commonly use alternate tools to complete tasks in the workplace. For instance, opting for a ladder instead of proper scaffolding on a construction site may offer initial savings, but it can also lead to reduced efficiency and increased danger. These factors can accumulate over time, resulting in greater costs overall.
It’s crucial to prioritize the use of tools specifically designed for the task, even if they’re more expensive initially. This choice will optimize productivity and enhance workplace safety in the long run.
5. Failing to invest in health and safety systems
When it comes to implementing new systems, companies may hesitate because of the necessary period of adjustment. However, recognizing the potential benefits such as improved efficiency and productivity, employers should prioritize implementation of appropriate systems for each job, including health and safety systems.
By using safety management software, companies can track all components involved and minimize the risk of making mistakes. This technology simplifies the process of maintaining compliance and ensuring employee safety by centralizing all the necessary data in a single space. As a result, companies can reap significant returns on investment while streamlining their operations and safeguarding their workforce.
Bottom line
It’s crucial for companies to prioritize implementing the right systems for each job, including robust health and safety systems, in order to avoid these common workplace safety mistakes and keep their people out of harm’s way. Despite the initial period of adjustment that may be required, the potential return on investment is significant. Leveraging a comprehensive EHS management solution can simplify the process by allowing companies to track all the moving parts and avoid costly mistakes. This technology centralizes data, making compliance maintenance and employee safety more streamlined. By investing in the right tools and systems, companies can optimize productivity, enhance workplace safety, and ultimately achieve long-term success.